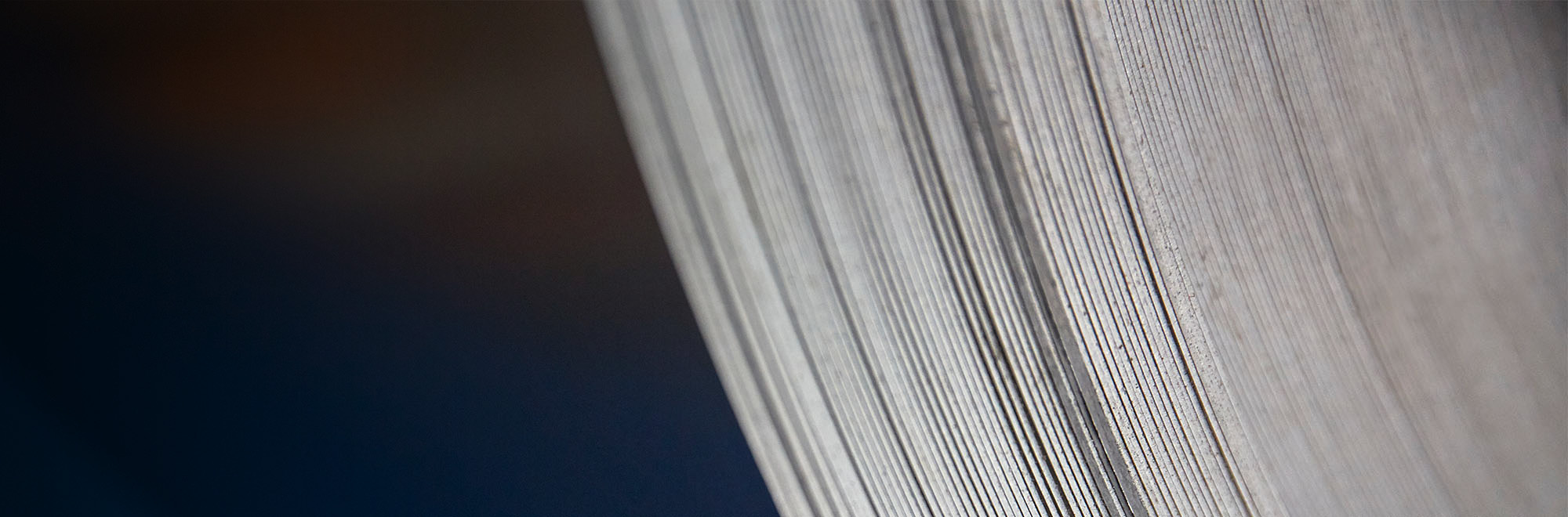
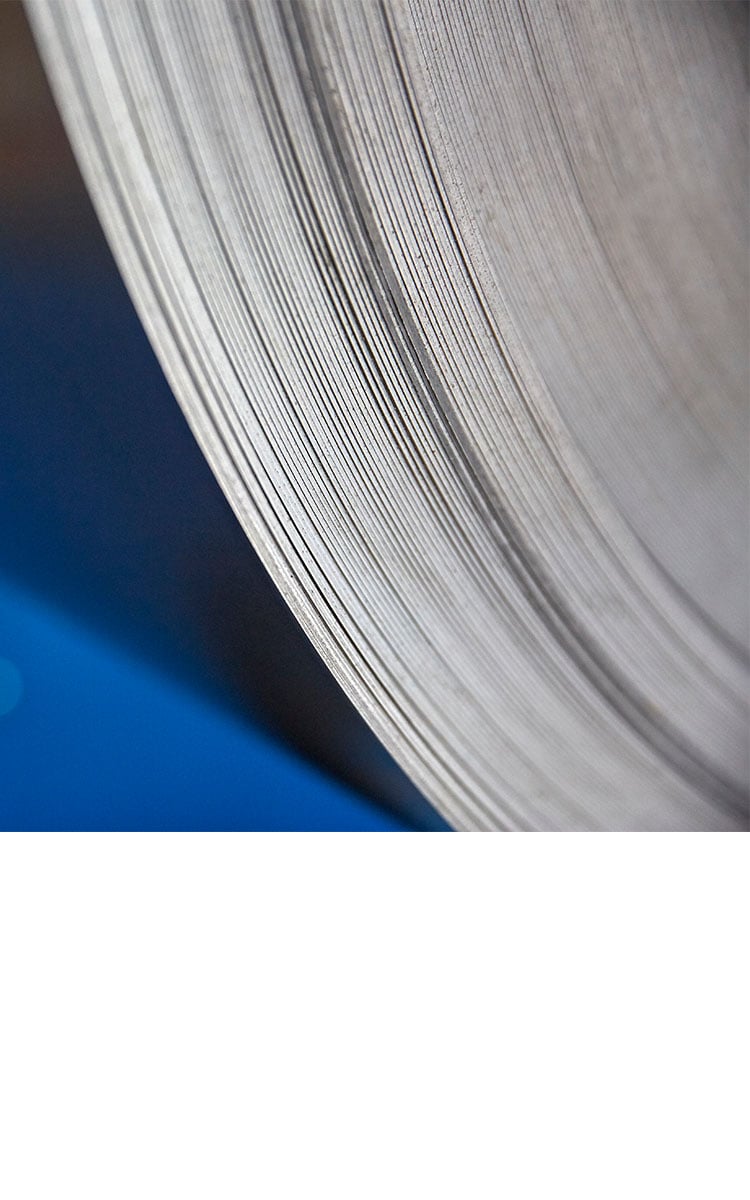
ARKU is the market leader for coil preparation & roll forming entry lines. These systems ensure that the strip preparation does not become a production bottleneck and guarantee that profile manufacturing pays off.
Contact usCoil Roll Forming Entry Lines for the continuous production of Profiles
Thorough coil preparation is essential to ensure high-quality results for the final products after roll forming. Short set-up times, constant up-times and the optimum interaction of all the components: ARKU roll forming entry lines guarantee maximum efficiency and continuous production. For economical roll forming.
ARKU is the world market leader for roll forming entry lines when it comes to coil processing. We have the right coil line for every roll forming task: from leveling, feeding, and control technology to intelligent punching solutions and interface integration for coil processing for roll forming lines all the way through to systems for pre-punching coil end welding.
Advantages of ARKU Roll Forming Entry Lines
Everything in one line
Decoiling, leveling, coil end welding, storage and pre-punching in a continuous line for roll forming. The complete solution for your strip preparation for roll forming.
Quick coil change
The TwinShuttle strip guide and the Weldomatic® coil end welding solution from ARKU ensure fast coil changes. By welding the coil strips together, allows for fast and efficient coil change without interupting production.
Your savings potential
We would be happy to calculate the individual cost savings based on your specific application.
A strong partnership
We have been working on fineblanking applications with the Feintool AG for more than 50 years. The global market leader for fineblanking presses, tools and peripheral systems.
ARKU Pre-punching Systems: all in one line
Pre-punching and roll forming strip materials with pre-punching systems from ARKU. The hydraulic punching units perforate the coils prior to roll forming.
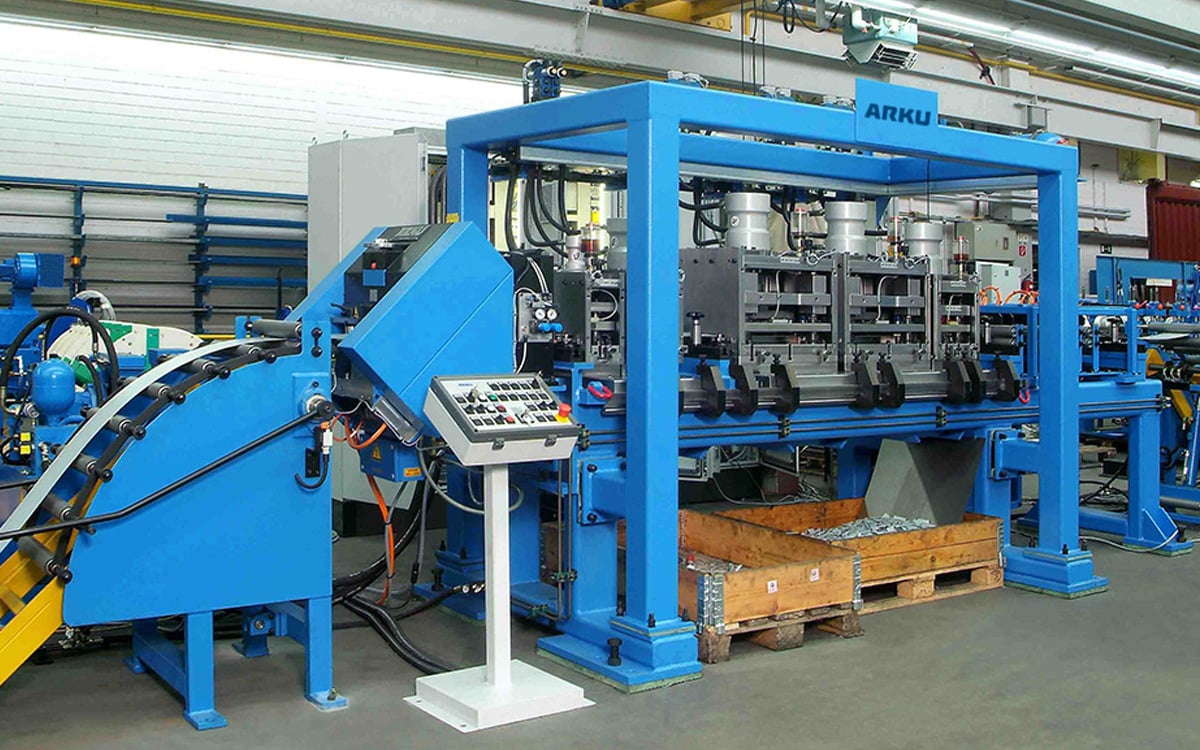
Facts at a glance
- Pre-punching and roll forming strip materials
- Hydraulic punching units perforate the coils prior to roll forming
Coil End Welding with the Weldomatic®: change Coils efficiently
The Weldomatic® coil end welding machine from ARKU reduces the downtimes of your roll forming entry lines. Especially when it comes to changing coils, long production downtimes occur due to the processing of the coil end and the time required for feeding in the new coil. The Weldomatic® automatically welds the old coil strip to the new coil strip when changing coils. Automated coil end welding can save up to 20 minutes, especially for complex systems with pre-punching operations. This enables coil change times of only 90 seconds. Because there is no need to punch the new coil, the Weldomatic® can also achieve material savings of up to 400%.
The Weldomatic® reliably welds coils made of steel, zinc, stainless steel, aluminum, copper and copper alloys. The modular design of the welding technology enables conversion or retrofitting for different various coil applications. In addition, the Weldomatic® coil end welders can also be integrated into every coil system, regardless of the manufacturer.
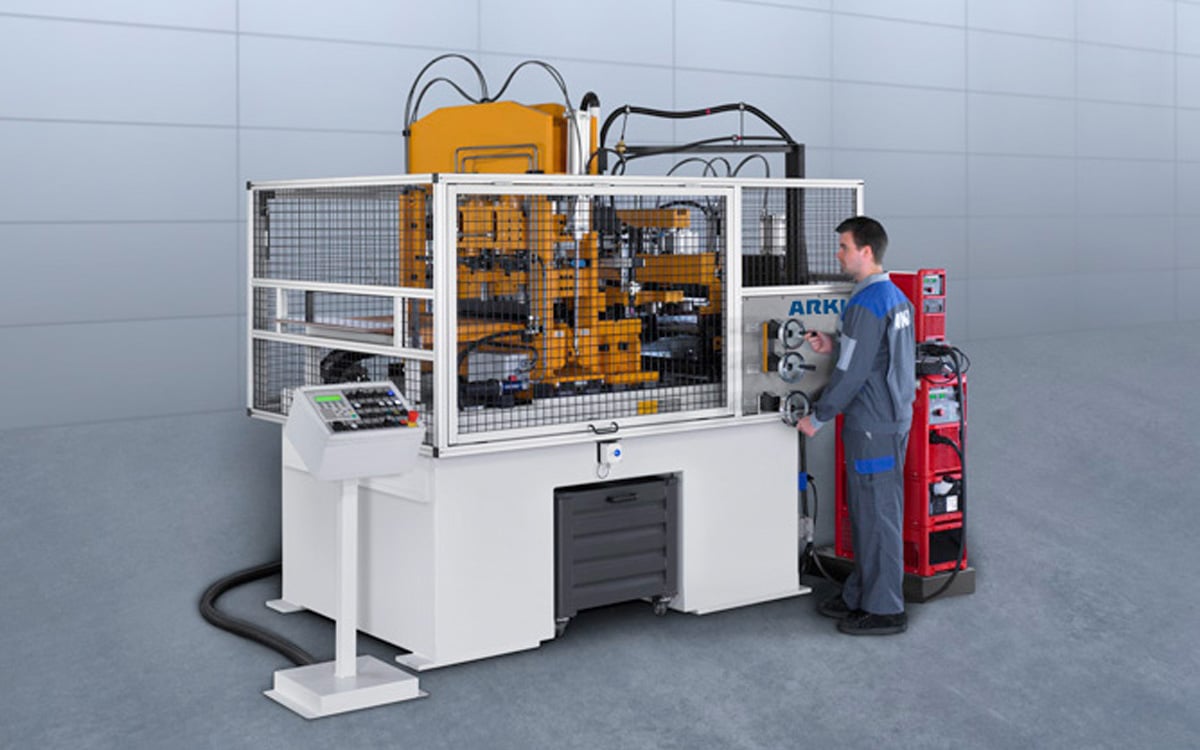
Facts at a glance
- Coil change related downtimes of less than 2 minutes
- Automatically welds the old coil strip to the new coil strip when changing coils
- Less material usage: savings of up to 400%
- No need to punch the new coil
- For diverse coil thicknesses ranging from 0.02" up 0.2" (0.5 up to 6 mm)