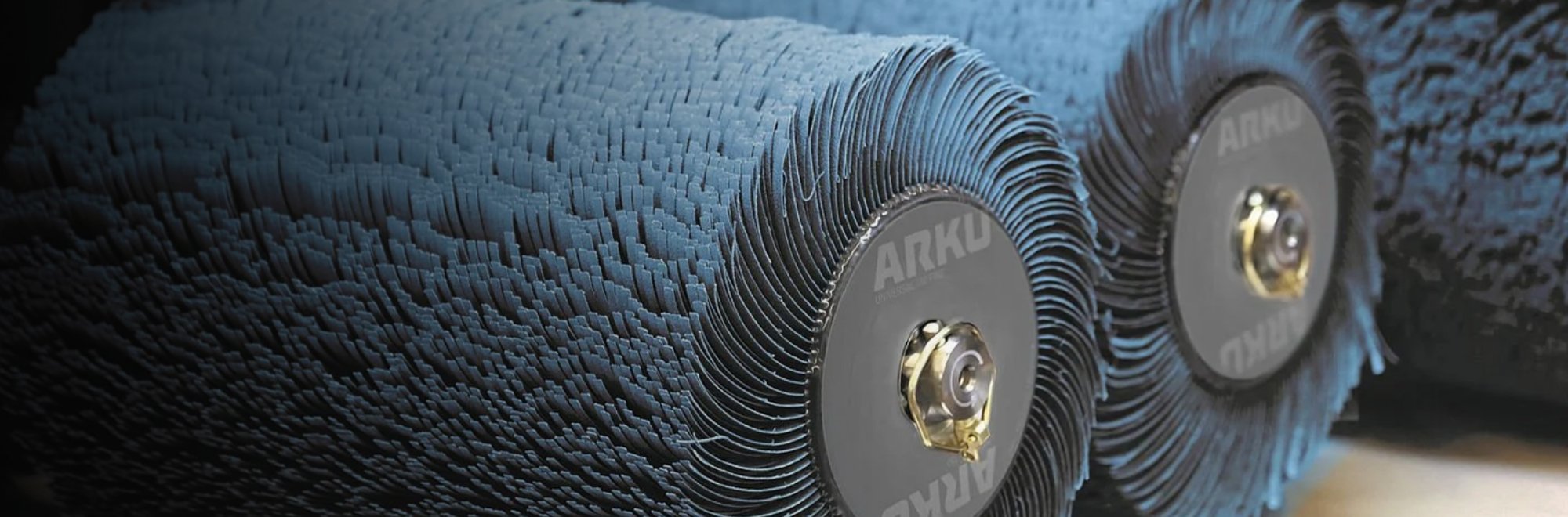
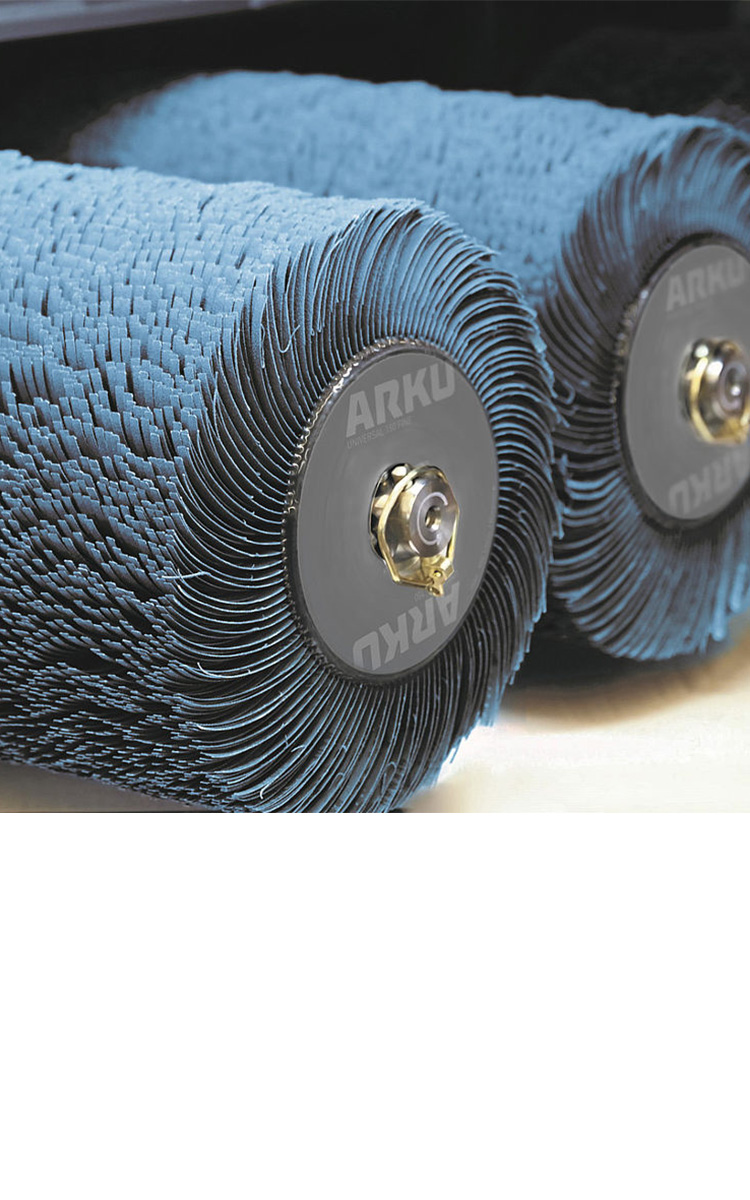
The complete deburring, edge rounding and surface finishing solution for sheet metal. Ideal for laser cut and punched parts. The high quality is achieved through eight abrasive rotary brushes which uniformly edge round the edges of the sheet metal perfectly.
REQUEST A QUOTEEdgeBreaker® 6000
Deburr, Edge Round & Surface Finish Punched & Laser Cut Parts with the Rotary Brush Machine
Your Advantages as an Overview
Wide processing spectrum for laser cut and punched parts
The EdgeBreaker® 6000 enables the processing of the widest possible range of sheet metal and sheet metal parts. Whether small sheet metal parts or large metal sheets, this deburring machine provides consistent high-quality results for deburring, edge rounding and surface finishing. The EdgeBreaker® 6000 is particularly suitable for laser-job shops with constantly changing processing requirements.
Achieve edge rounding results of up to 2 mm
The most striking unit in the EdgeBreaker® 6000 makes it possible: the rotary brushes. These rotary brushes achieve a unique edge rounding along the sheet metal edges. As the brushes hit the sheet metal in various directions, you can achieve a very uniform result on the inner and outer contours. If necessary, an edge rounding radius of up to 2 mm is possible.
Quick-change for deburring, edge round and surface finishing tools
All processing units (deburring, edge rounding and surface finishing) are equipped with a quick-change system for the tools (abrasives) to minimize set-up times. You can simply remove the belts and rotary brushes, without any tools needed! The machine can be outfitted with a variety of different tools (various grits and material composites are available). All for optimum deburring, edge rounding, and surface finishing results to suit your changing requirements.
Consistent results for every part thanks to automatic wear compensation for abrasives
For consistent results, it is essential to always know where you stand. The EdgeBreaker® 6000 measures the remaining length of your tools (abrasives), in this case the rotary brushes, within the machine and automatically compensates for the wear off. Leaving you with consistent results from beginning till end of the tools life.
Simple operation and maintenance for the deburring machine
The graphical touchscreen HMI is very intuitive and easy to operate. It supports you in setting up the machine and provides tips on operation and maintenance. it can even be used while wearing safety gloves. For efficient processing without errors.
Tool storage for saving processing parameters
If you produce a particular sheet metal part from time to time, you can save the processing settings diretly in the machine and call upon the values when required. This allows you to quickly setup the deburring machine for repeat production runs. Thus, avoiding errors during setup.
See for yourself: the Video of the EdgeBreaker® 6000!
The EdgeBreaker® 6000 deburring machine optimally prepares your punched parts or laser cut parts for further processing. All burrs are removed, the edges are rounded more evenly than with any other process and, if desired, you can also apply a special surface finish.
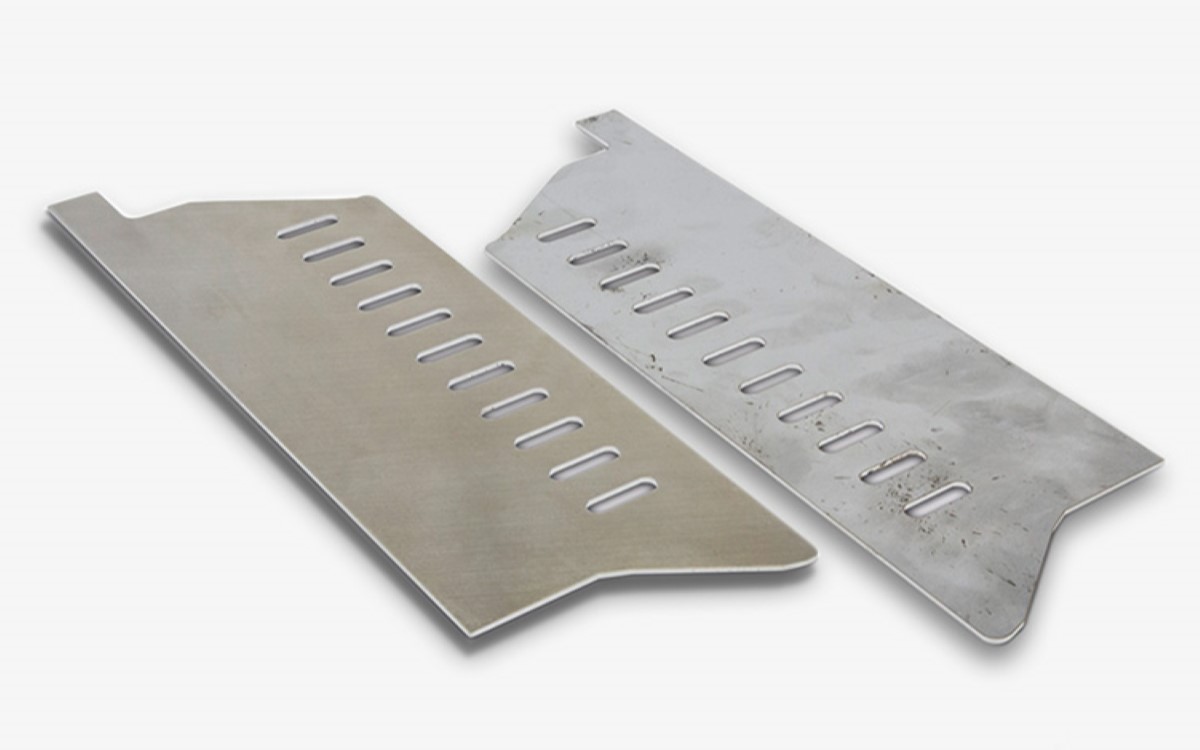
Punched and Laser Cut Parts: the Complete Processing with the EdgeBreaker® 6000 Rotary Brush Machine
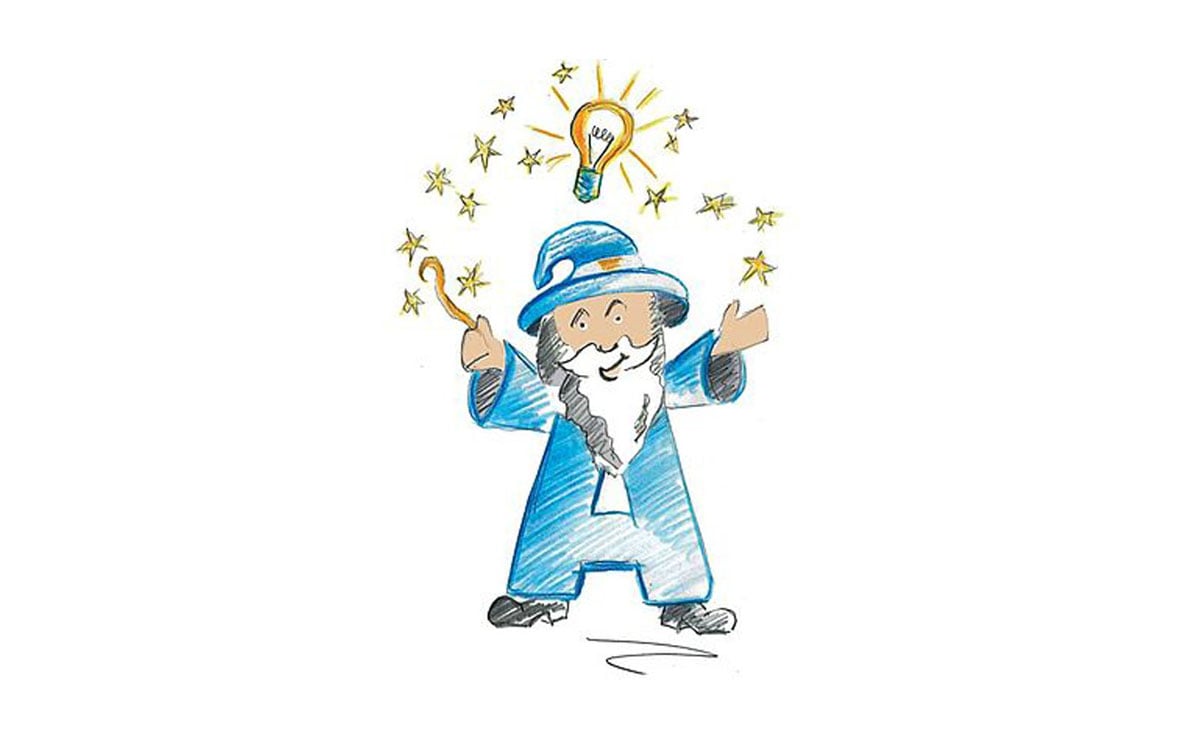
Always the Ideal Processing Settings – with the ARKU Wizard
The ARKU Wizard is an intelligent software that helps its operators to automatically adjust the processing settings of their deburring machine. During the process, the material, tool and machine data are linked together. Only four parameters (material, size of burrs, material thickness, desired edge rounding) need to be entered. The tools available to the operator are stored in the Wizard. The software automatically selects the best deburring tool for the particular processing requirement(s). In doing so, the Wizard always optimally adjusts the deburring machine to achieve maximum productivity and minimal tool wear. In this way, operators can be sure of achieving the desired processing results with minimum effort and no time wasted.
Processing Features for every Requirement
ARKU has developed various modules for processing sheet metal parts to ensure the highest quality, reliable processes and individual, tailor-made solutions that meet your requirements.
Previously, we did all of our deburring by hand, so we wanted to eliminate that physically demanding part of our job and redirect human resources to where they are really needed.“Jordan Yost, Co-Owner of Precision Tube Laser, Las Vegas (USA)
Technical Data Overview
Processing | single-sided, dry |
Material thickness | up to 1" (25 mm) |
Max. working width | 51" (1,300 mm) |
Weight | approx. 14,300 lbs (6,500 kg) |
Dimensions (L x W x H) | approx. 165" x 83" x 93" (4,200 x 2,100 x 2,350 mm) |
Do you have different requirements? We would be happy to support you with a customized solution.
Please contact us!
Frequently Asked Questions
Suitable Tools
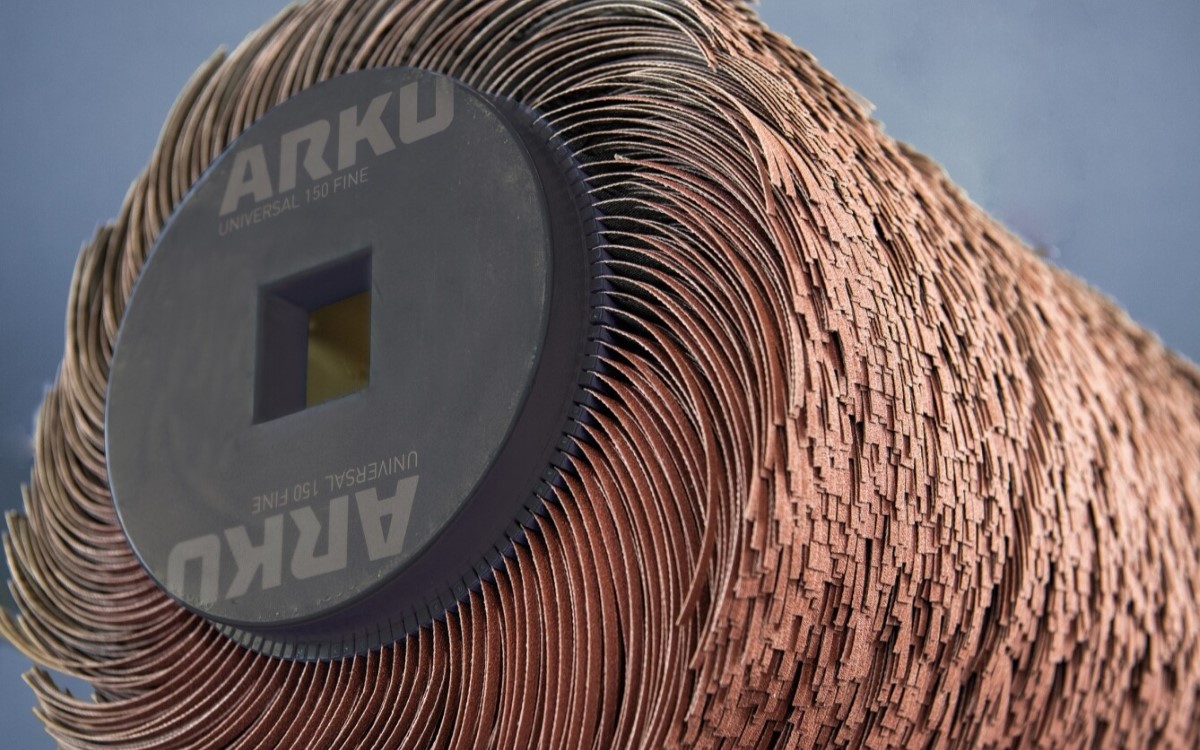
Rotary brushes for edge rounding
From the universal original to the custom-made tool for your specific application.
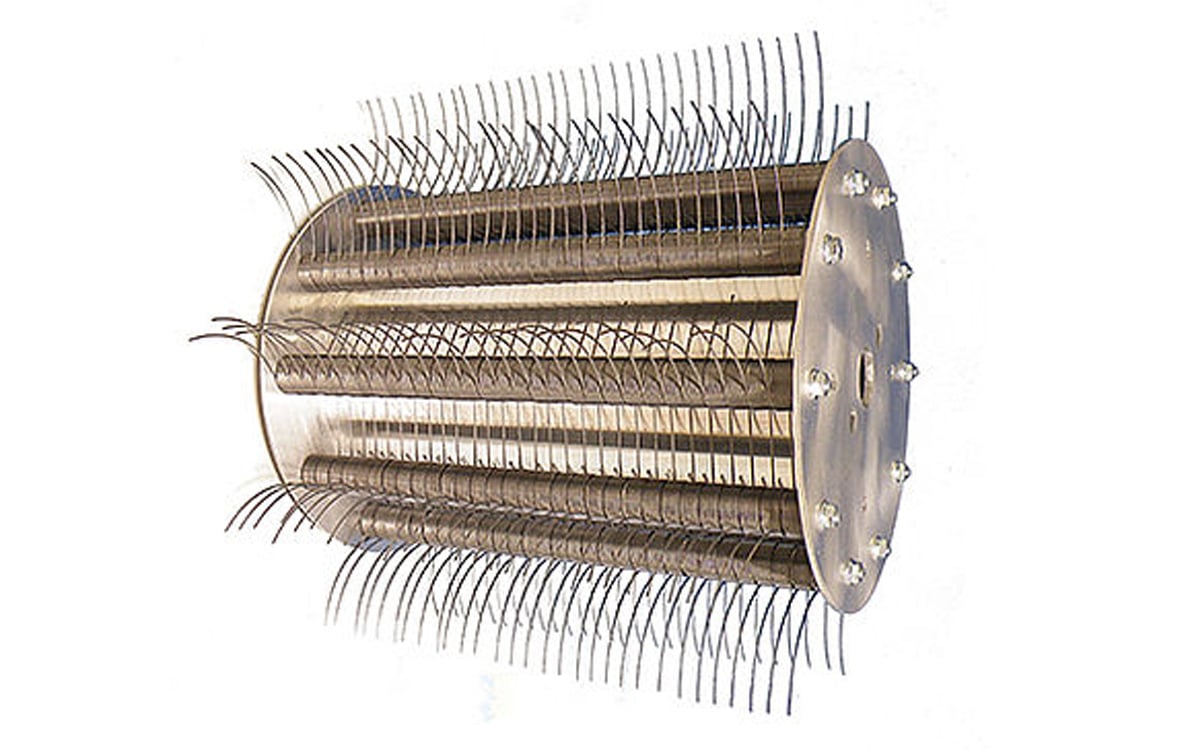
Roller brushes for oxide removal
A special purpose tool for the removal of oxide byproducts from your cutting edges.
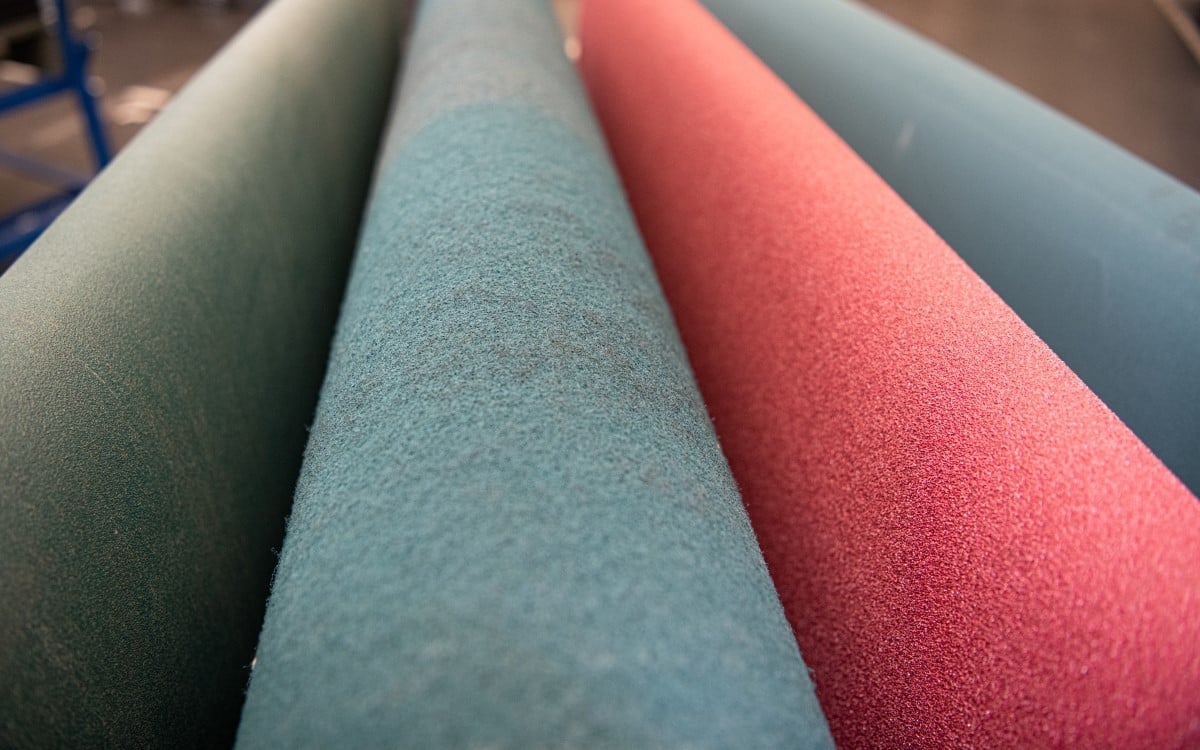
Abrasive belts for deburring
Abrasive belts to deburr sheet metal parts.
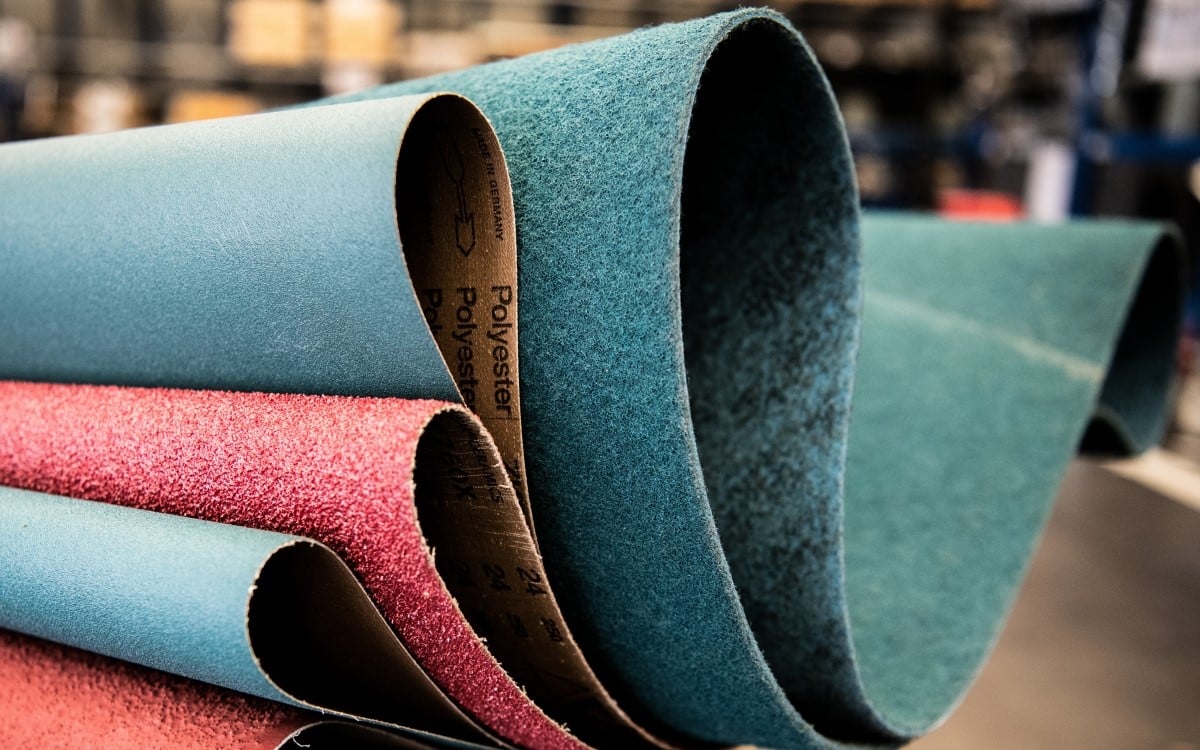
Non-woven abrasives
Non-woven abrasives for surface finishing.
Suitable Tools
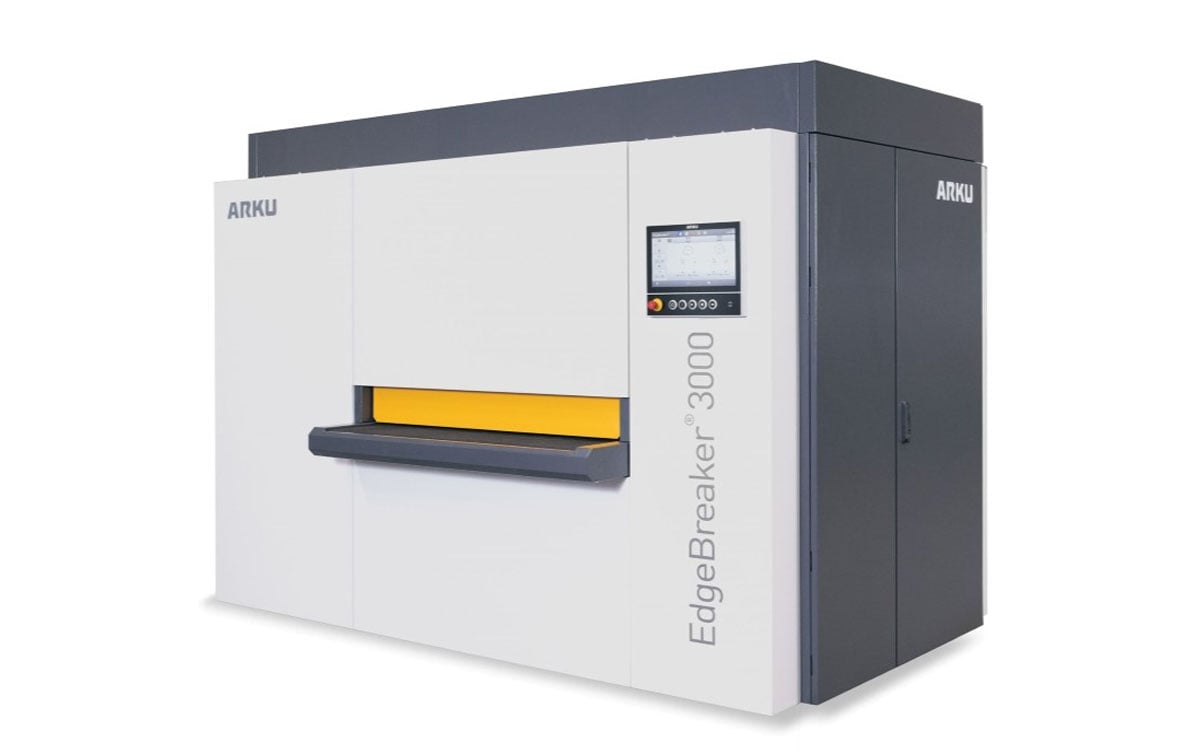
EdgeBreaker® 3000 NEXT
Powerful workhorse for maximum throughput – deburrs and edge rounds top and bottom in a single pass.
Material thickness: 0.03" - 4" (0.8 - 100 mm).
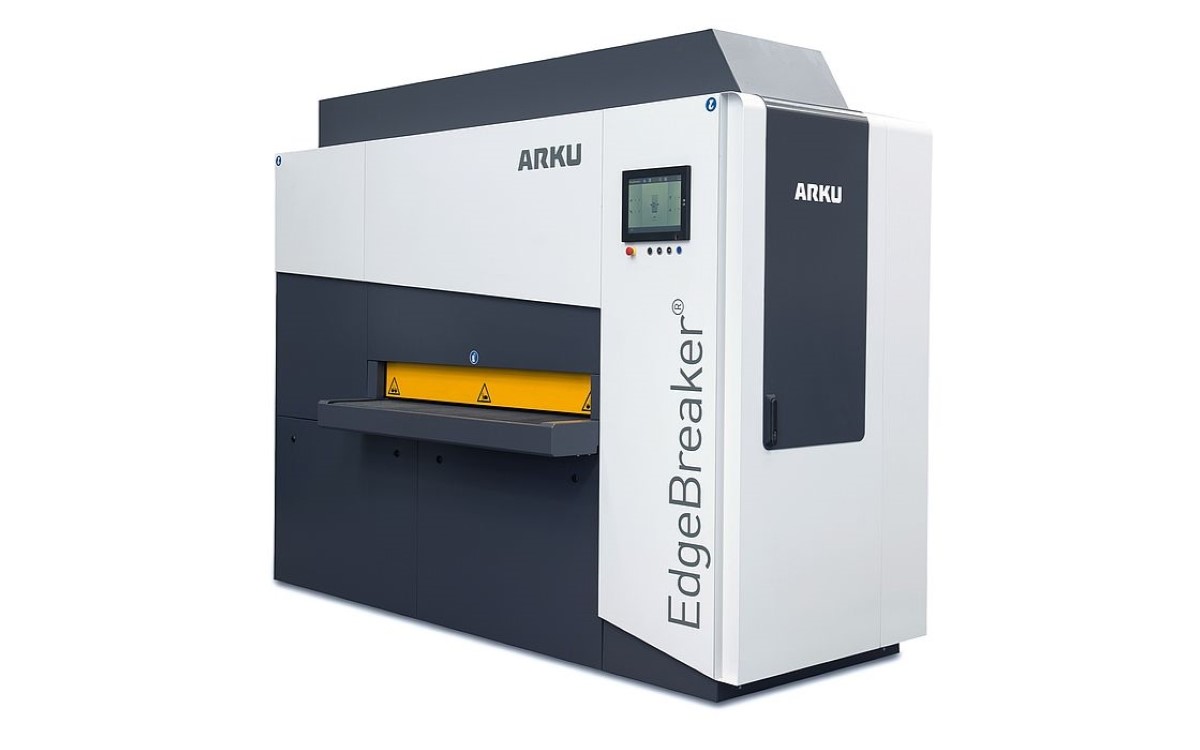
EdgeBreaker® 2000
The double-sided edge rounding expert that can also deburr.
Material thickness: 0.03" - 4" (0.8 - 100 mm).
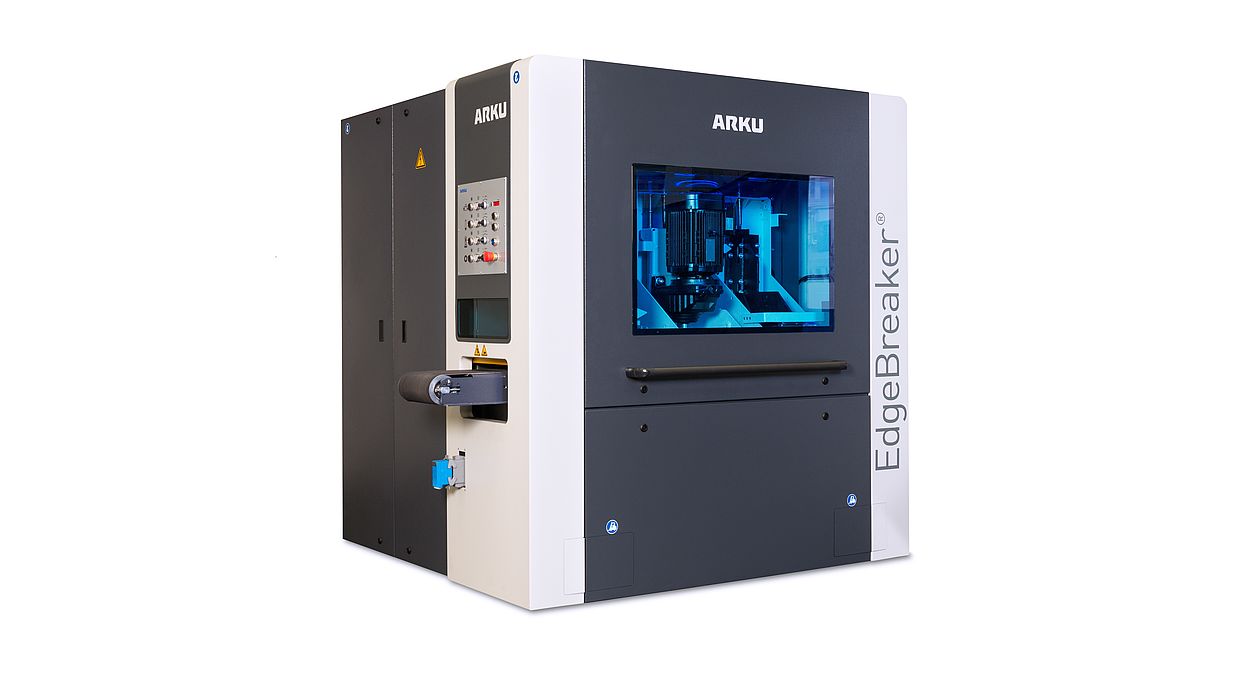
EdgeBreaker® 1000
Specialist for the economic processing of small parts. Deburring, edge rounding and finishing.
Material thickness: 0.02" - 1" (0.5 - 25 mm).