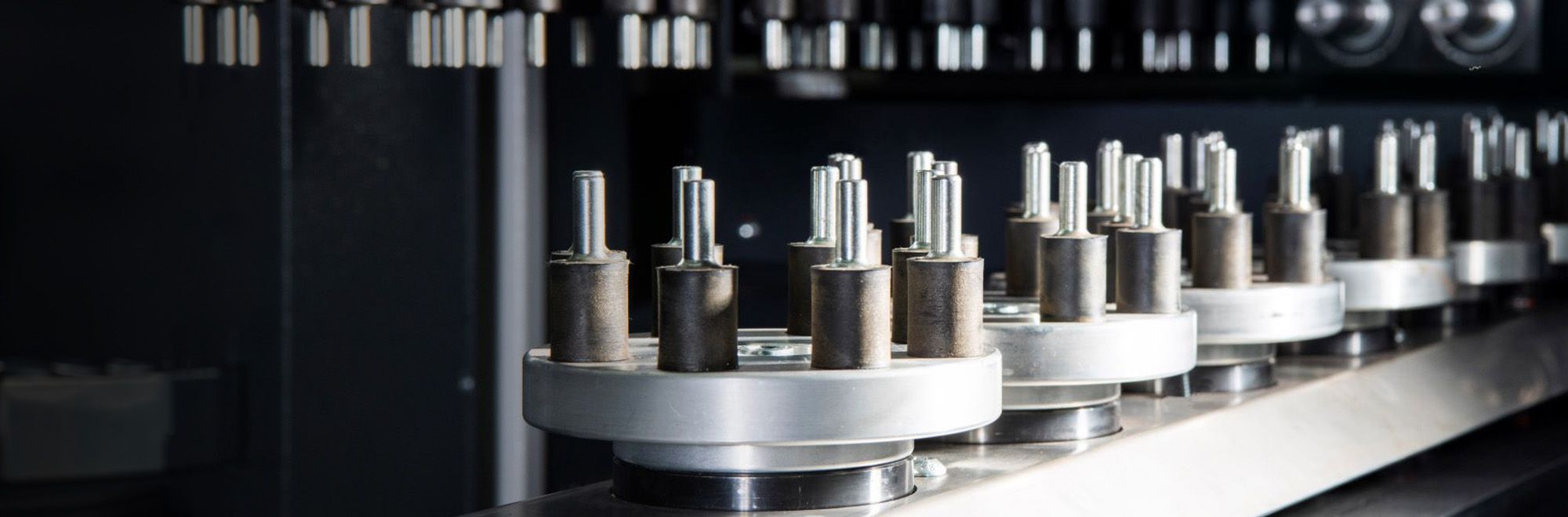
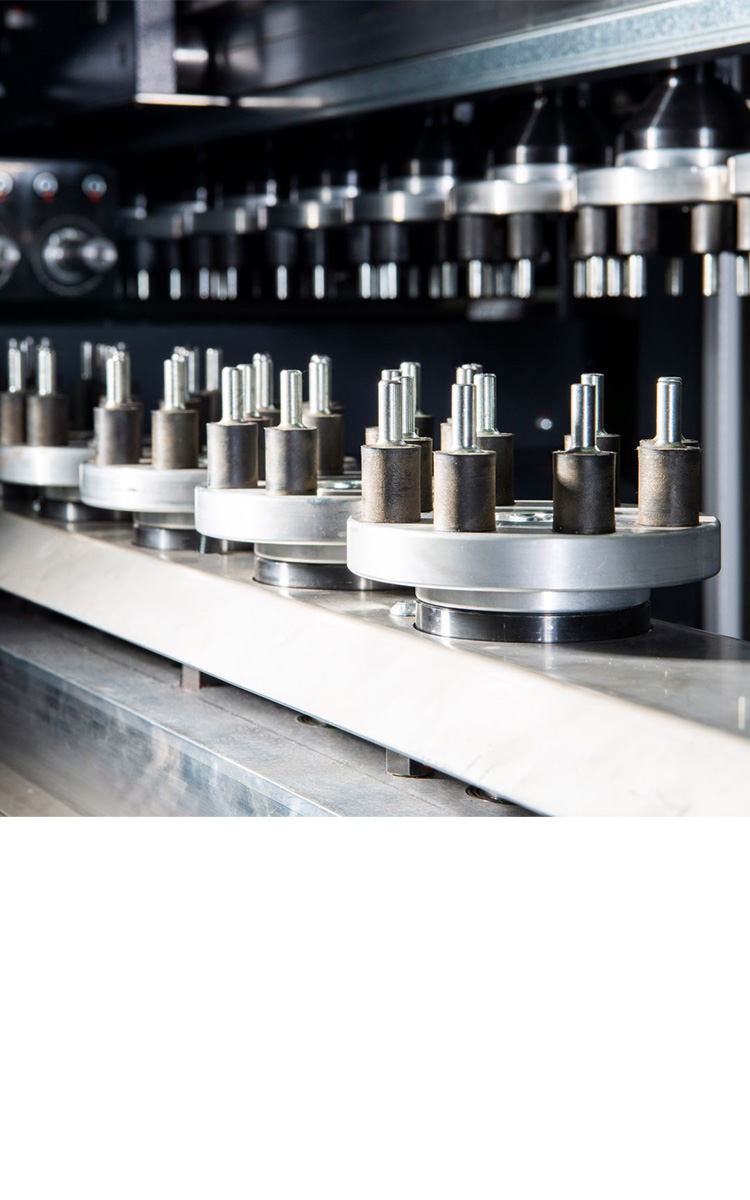
Efficiently eliminate slag and dross accumulated on metal parts & plates from plasma, flame or oxyfuel cutting with our automated slag removal machine. Double or single-sided slag removal available.
REQUEST A QUOTEEdgeBreaker® 5000 MAX
Single-sided & Double-sided Slag Removal Machine for Metal Plate & Parts
Your Advantages as an Overview
No turning over of heavy plasma and flame cut parts
The EdgeBreaker® 5000 MAX removes the slag where it is produced: on the underside of the materials. In contrast to manual processing of heavy plate, it is therefore not necessary to turn over any heavy parts, thus avoiding injuries! Mechanical slag removal therefore reduces the strain on employees and increases work safety. If required, the slag can also be removed from top side as well. All in just a single pass.
Remove metal slag and dross reliably
With the pins fixed to discs inside the machine, slag is removed more reliably than ever before. It creates saftey for the entire deburring process.
Quick-change for all tools
All tools (pin discs outfitted with slag hammer pins) are equipped with a quick-change system. This minimizes your set-up times, increases productivity and lowers downtime.
Simple operation and maintenance for the deslagging machine
The graphical touchscreen HMI is very intuitive and easy to operate. It supports you in setting up the machine and provides tips on operation and maintenance. It can even be used while wearing gloves. For efficient processing without errors.
Small parts processing capable
Even small parts can be processed safely with the EdgeBreaker® 5000 MAX. A small parts guide ensures reliable processing from either side.
See for yourself: the Video of the EdgeBreaker® 5000 MAX!
The pins mounted to the discs within the EdgeBreaker® 5000 MAX leave slag and dross no chance. The video clearly demonstrates how the slag hammers completely removes these remnants after the cutting process. Any remaining pieces of lighter slag or even burrs that cannot be knocked off; are ground off in the next step using a deburring machine.
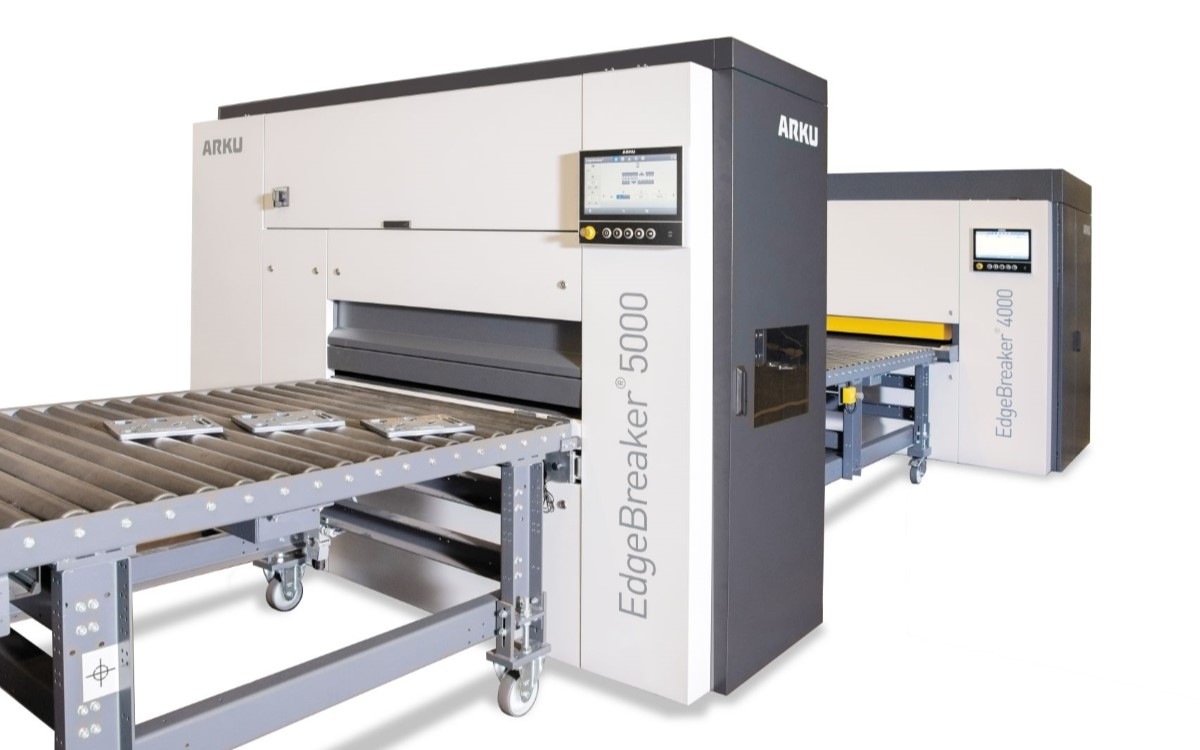
Deburring Machine that can be Linked with other Machines
Before you can deburr and edge round heavy plate and plasma, flame (oxyfuel) cut parts, you need to remove the slag and dross first. This task is ideal for the EdgeBreaker® 5000 MAX deslagging machine. It can be combined with the EdgeBreaker® 4000 deburring machine for the complete processing of flame-cut parts in a single pass. This saves time and costs.
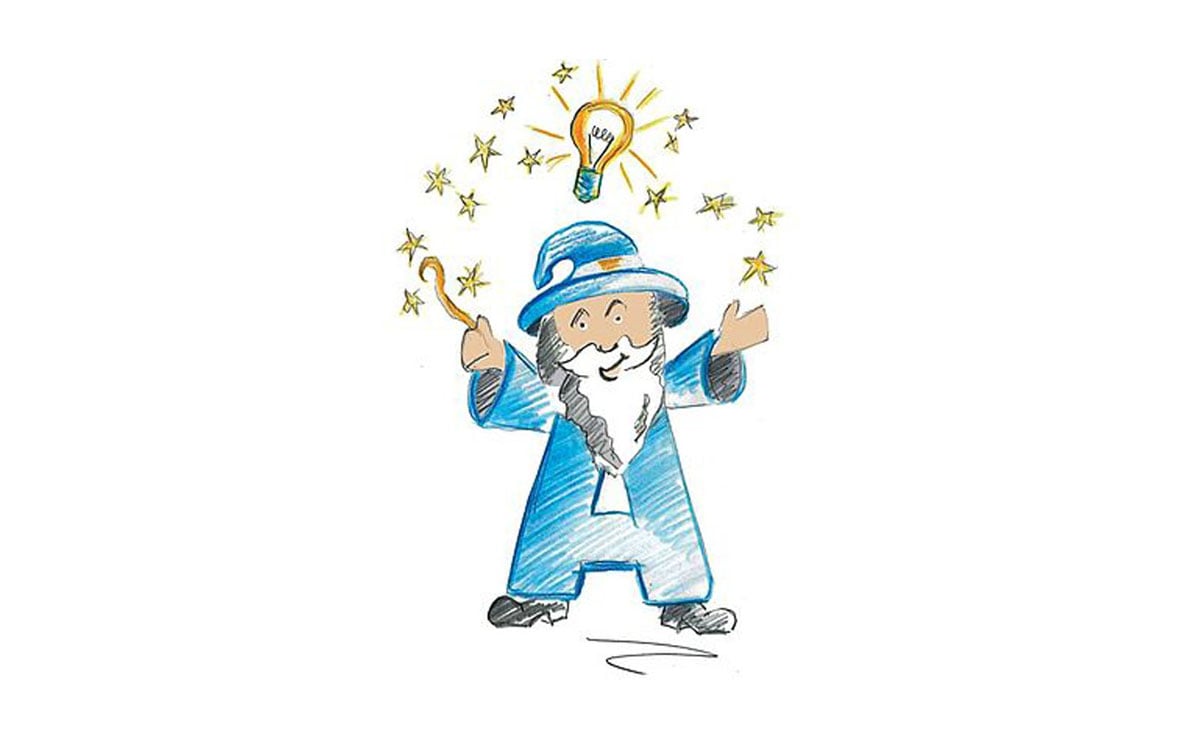
Always the Ideal Processing Settings – with the ARKU Wizard
The ARKU Wizard is an intelligent software that helps its operators to automatically adjust the processing settings of their deburring machine. During the process, the material, tool and machine data are linked together. Only four parameters (material, size of burrs, material thickness, desired edge rounding) need to be entered. The tools available to the operator are stored in the Wizard. The software automatically selects the best deburring tool for the particular processing requirement(s). In doing so, the Wizard always optimally adjusts the deburring machine to achieve maximum productivity and minimal tool wear. In this way, operators can be sure of achieving the desired processing results with minimum effort and no time wasted.
Processing Features for every Requirement
ARKU has developed various modules for processing sheet metal parts to ensure the highest quality, reliable processes and individual, tailor-made solutions that meet your requirements.
Technical Data Overview
Processing | single-sided, from the bottom (optionally double-sided) |
Material thickness | 0.39" - 4.92" (10 - 125 mm) |
Max. passageway width | 51" - 79" (1,300 - 2,000 mm) |
Weight* | approx. 3,800 kg (8,400 lbs) |
Dimensions* (L x W x H) | approx. 118" x 47" x 91" (3,000 x 1,200 x 2,300 mm) |
* with 51" max. passageway width
Do you have different requirements? We would be happy to support you with a customized solution.
Please contact us!
Frequently Asked Questions
Related machines
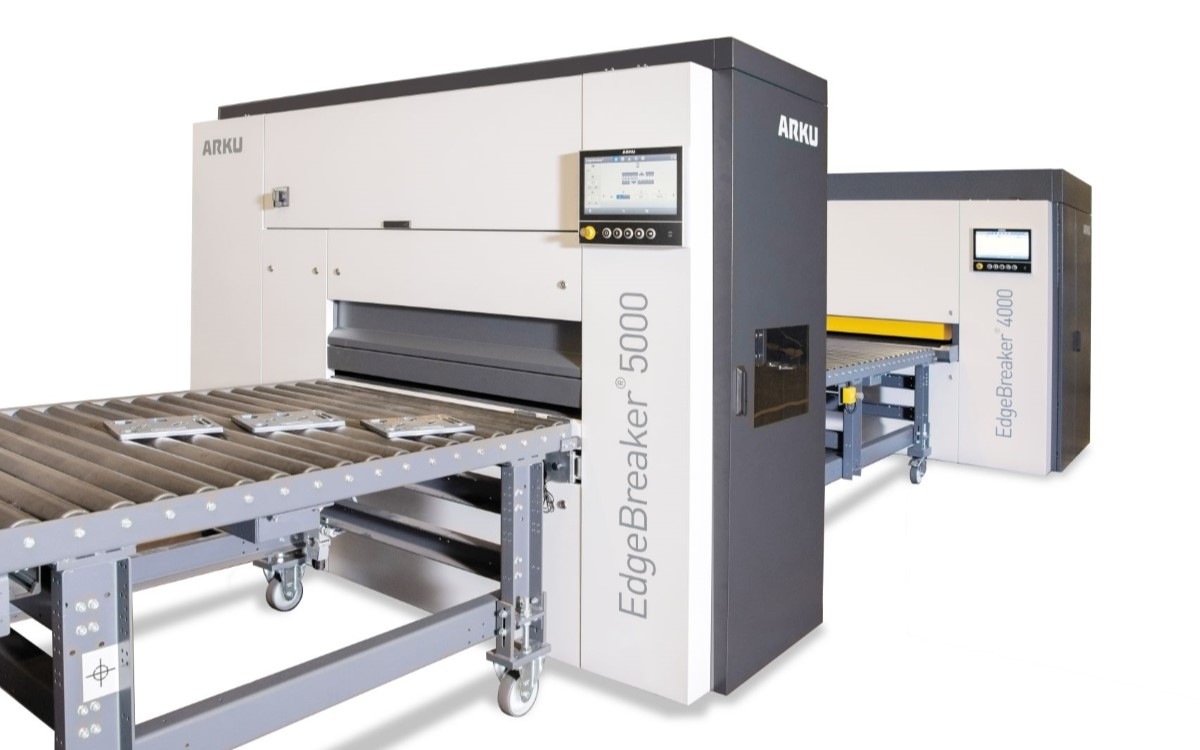
EdgeBreaker® 9000 LINE
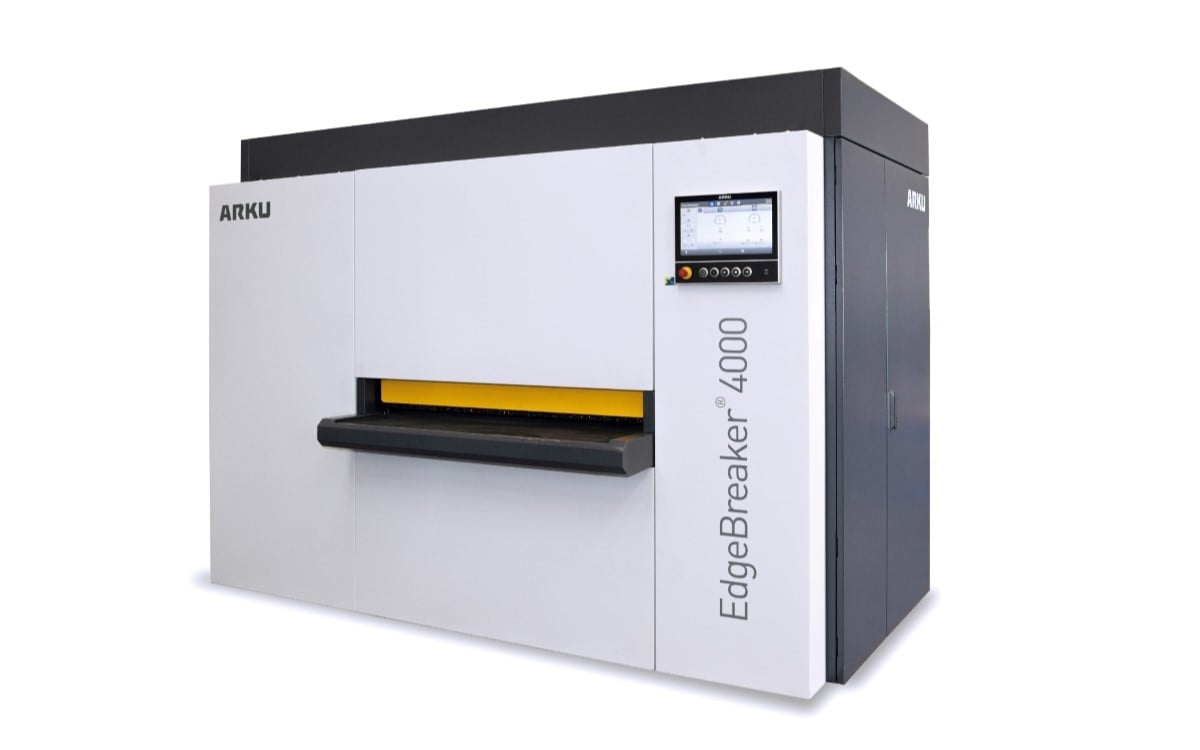
EdgeBreaker® 4000
The ultimate powerhouse for flame cut parts featuring a heavy-duty grinding drum.
Material thickness: 0.03" - 4" (0.8 - 100 mm).