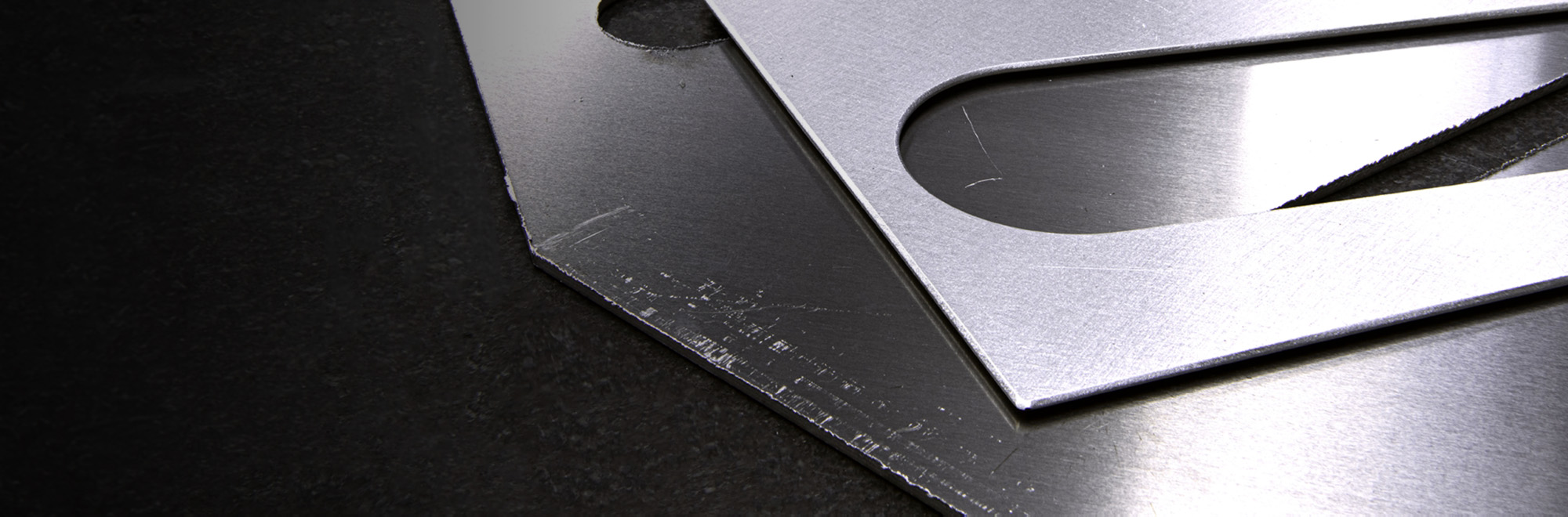
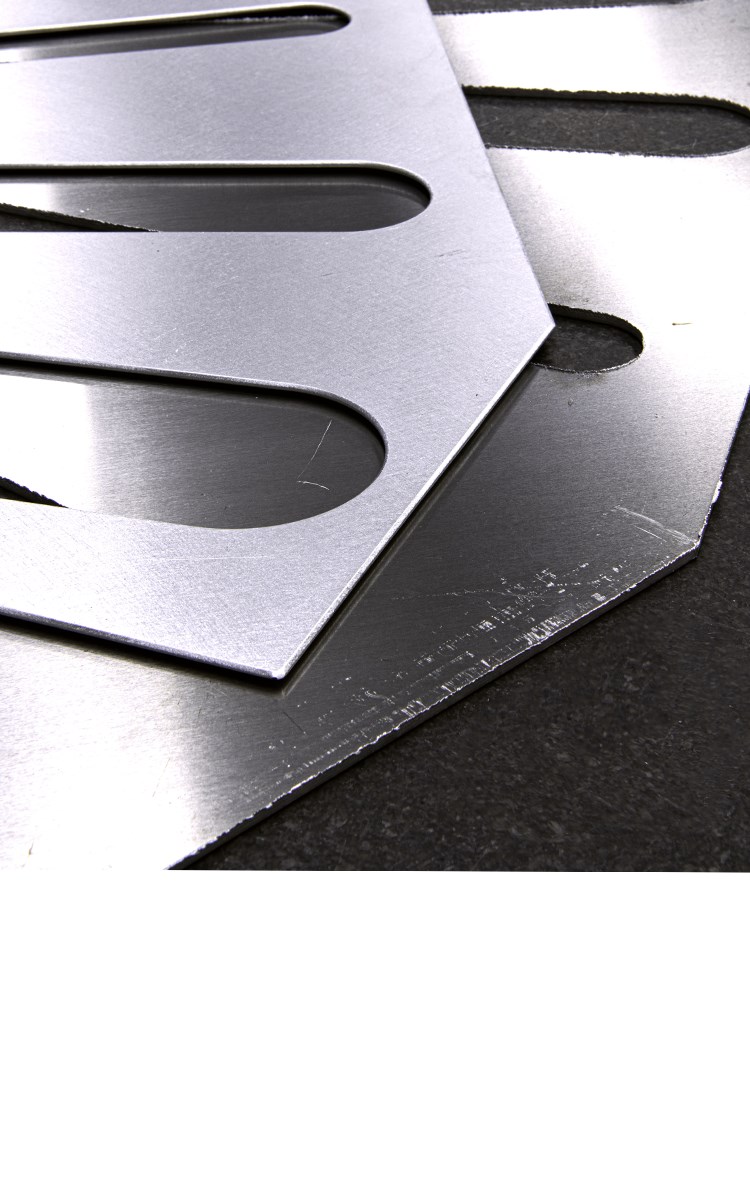
Sheet metal finishing is an important step during manufacturing. It allows for raw parts and sheets to be refined into superior products with enhanced appearance and functionality. Various finishes like a grain finish for example can be applied.
Straight to the machines?Surface Metal Finishing Process & Solutions
How is the Surface of Sheet Metal processed in the Deburring Machine?
The surface finishing options in a deburring machine are limited. These processing units in deburring machines are not suitable for a specific surface finishes, as is also known from steel service centers. Nevertheless, an additional wide belt unit and the corresponding nonwoven abrasive fleece can be used to improve the sheet surface after deburring and edge rounding. Various nonwoven surface finishing fleeces are available in our webshop. By selecting the "grain size", you determine the roughness or structure of the surface. This allows you to achieve the desired surfaces for further processing for common sheet metal applications. The surface treatment units and processes presented here are specifically designed for this purpose.
What are the Advantages of Surface Finishing Sheet Metal?
Improved paint adhesion
A rough surface is particularly suitable for paint adhesion.
Aesthetics
Finely polished sheet metal parts have a particularly attractive appearance.
Surface Finishing Sheet Metal with a Roller Fleece Brush
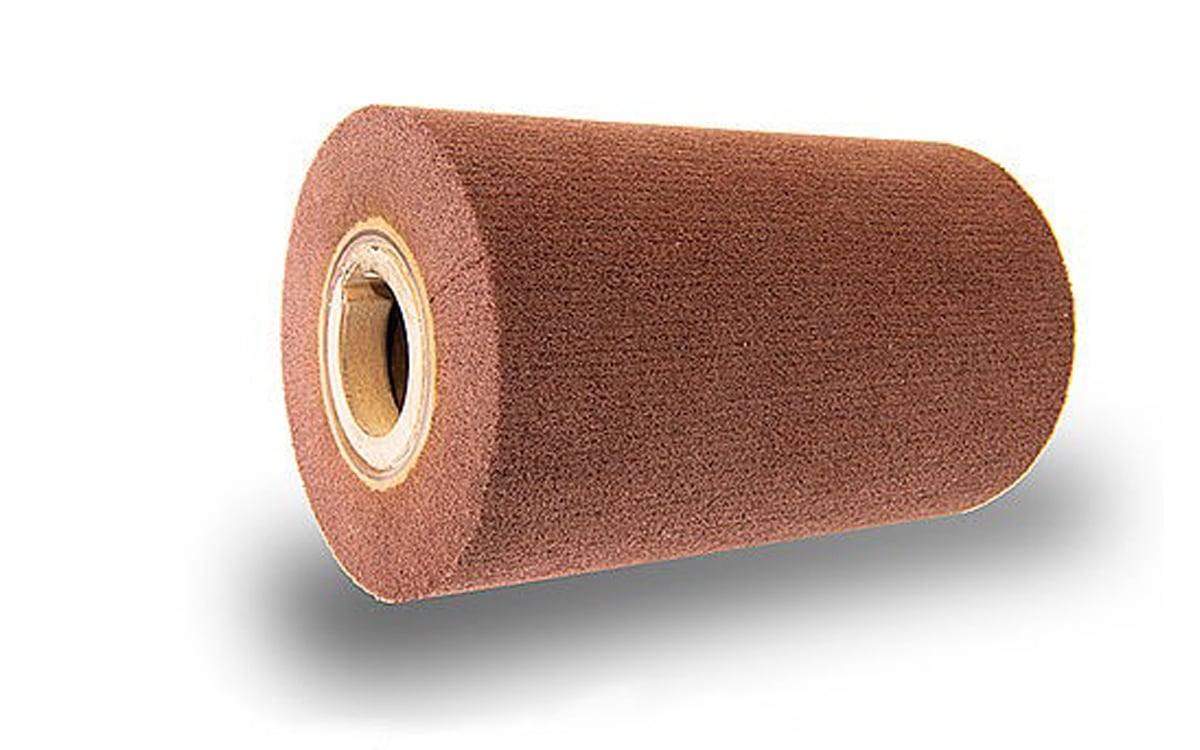
Facts at a glance
- The roller fleece brush consists of a core which is surrounded by abrasive fabric.
- The roller fleece brush produces a very uniform finish on sheet metal.
- The surface finishing results can be influenced by the choice varying abrasive material and grit of the roller fleece brush.
Suitable machines
Surface Finishing Sheet Metal with a Wide Belt
The final surface result is a combination of the machine, tools, processing settings, and throughput speed.
Facts at a glance
- Wide belt units are most frequently used for surface finishing sheet metal.
- Scratches are removed from the surface via the surface finishing fleece.
- The abrasive fleece used influences the removal rate and roughness of the surface.
- Abrasive non-woven fleeces are available in various abrasive materials and grits.