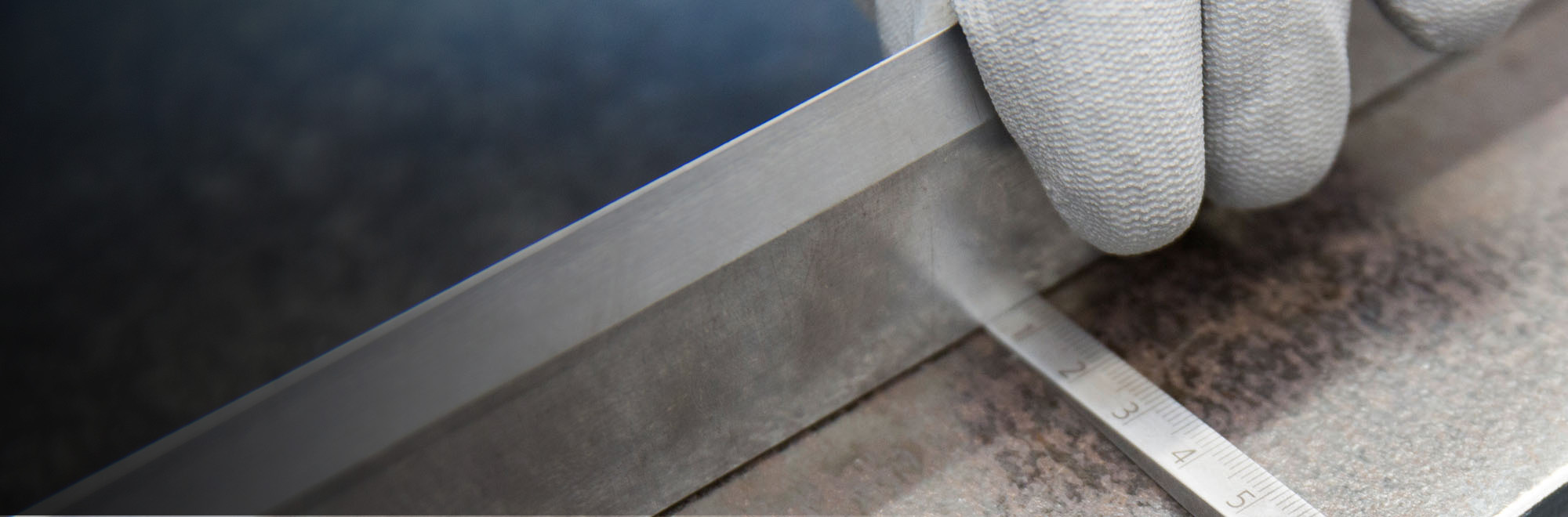
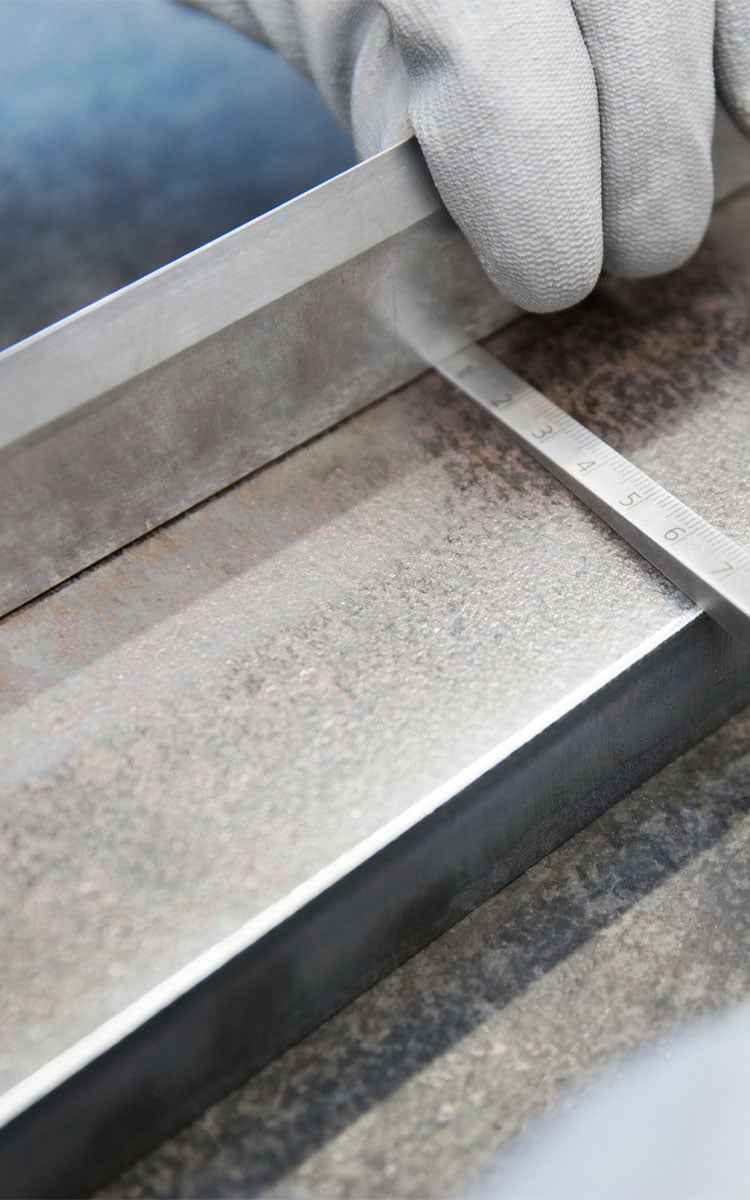
Remove residual stresses and flatness deformities from parts, sheet metal and heavy plate for efficient downstream processing.
Straight to the machinesSheet Metal & Heavy Plate Leveling Process
If you want to produce perfect metal parts and assemblies with tight tolerances from sheet metal or heavy plate, you have to be able to rely on the material. This cannot be taken for granted: many parts or sheets contain residual stresses and unevenness and these interfere with efficient further processing.
Residual stresses in sheet metal can arise in different ways: by using thermal cutting processes like laser, flame and plasma cutting, introduces a high amount of heat into the material at the cutting beam. The resulting temperature gradient in the material causes stresses and hardening along the edges. As a result, the metal parts are warped after cutting. During punching, the sheet metal part is deformed by the punching process and existing internal stresses in the material are released.
How to Flatten and Remove Residual Stresses from Sheet Metal and Heavy Plate?
There is only one way to safely eliminate residual stresses: leveling. In a roller leveling machine, the material goes through several successive alternating bends. As a general rule, the more alternating bends, the better the leveling result. Afterwards you can be sure that your sheet metal parts or heavy plate will retain the desired shape and that your downstream processes will be improved dramatically. Welding times and results will be a day and night difference when working with not leveled materials.
As a general rule of thumb, all metals with an elongation at break of at least five percent and a pronounced yield strength are suitable for leveling. If these values are not known, the suitability for leveling can be determined by leveling tests. The rule of thumb is: if it can be bent, it can be leveled. The situation is different for hardened materials: if the material has an elongation at break after the hardening process, it can be assumed that it can be leveled to a certain extent. However, high forces in conjunction with small roller diameters are required to deform such materials. If the material has no elongation at break, there is a risk of cracking or even breakage. In such cases, only leveling tests can show whether leveling is possible and what results can be expected.
What Solutions are there to Level my Sheet Metal and Heavy Plate?
In addition to roller levelers, there are other straightening methods. Straightening with a hammer and flame, for example, is very time-consuming and requires a lot of experience. Some sheet metal workers simple plate rolls to eliminate flatness deformations. Although this solution brings visible improvements, residual stresses in the material are hardly reduced. The use of manual straightening presses is similarly complex to that of plate rolls. These manual straightening presses are often used for heavy plate and parts with thicknesses over 60 mm. With this process, a processing time of up to 20 minutes per part is not uncommon.
In a precision leveler, also known as a roller leveler, rollers bend the sheet metal or heavy plate alternately upwards and downwards until it is straight and stress-free. There are mechanically or servo-hydraulically operated roller levelers. Mechanical roller levelers quickly achieve the desired result for parts with lower flatness requirements. For tighter requirements, the sheet metal parts often have to be leveled several times. Servo-hydraulic roller levelers are designed for tighter flatness requirements. The straightening rollers are optimally supported and have a small gaps between them. The integrated straightening gap control keeps the straightening gap constant during the entire straightening process, even with changing part cross-sections. Even difficult flame-cut parts can be level and stress-free within a few minutes.
What are the Advantages of Flattening Metal with a Roller Leveler?
Eliminate residual stresses and unevenness
Rolling, mechnical or thermal cutting processes and the effects of heat can lead to residual stresses within the material. You can reliable eliminate these internal stresses with a roller leveler.
Avoid manufacturing errors and rework
Residual stresses in the sheet metal lead to angularity errors during bending or distortion during welding. You can avoid these difficulties right from the start by leveling your sheet metal or heavy plate.
Meet tight tolerances
During assembly, it sometimes becomes apparent that the tolerances add up to too much. If you manufacture as precisely as possible right from the start, you won't get into this predicament. This is possible with leveled and stress-relieved sheet metal parts and heavy plate.
Fewer rejects with welding robots
For efficient production, welding robots require sheet metal parts with particularly tight tolerances. It is therefore important to flatten these parts before feeding them to the robot. Otherwise there is a risk of too many rejects and a standstill of the robot.
During machine flattening with straightening rolls (roller leveling), a sheet metal part or heavy plate passes through several successive alternating bends. The straightening rolls are offset from the inlet to the outlet of the roller leveler. This means that one roll always dips between the two opposite straightening rolls. The alternating bends are strong at the first straightening rollers and become increasingly weaker towards the outlet. The course of the bends thus resembles a decaying sine curve.
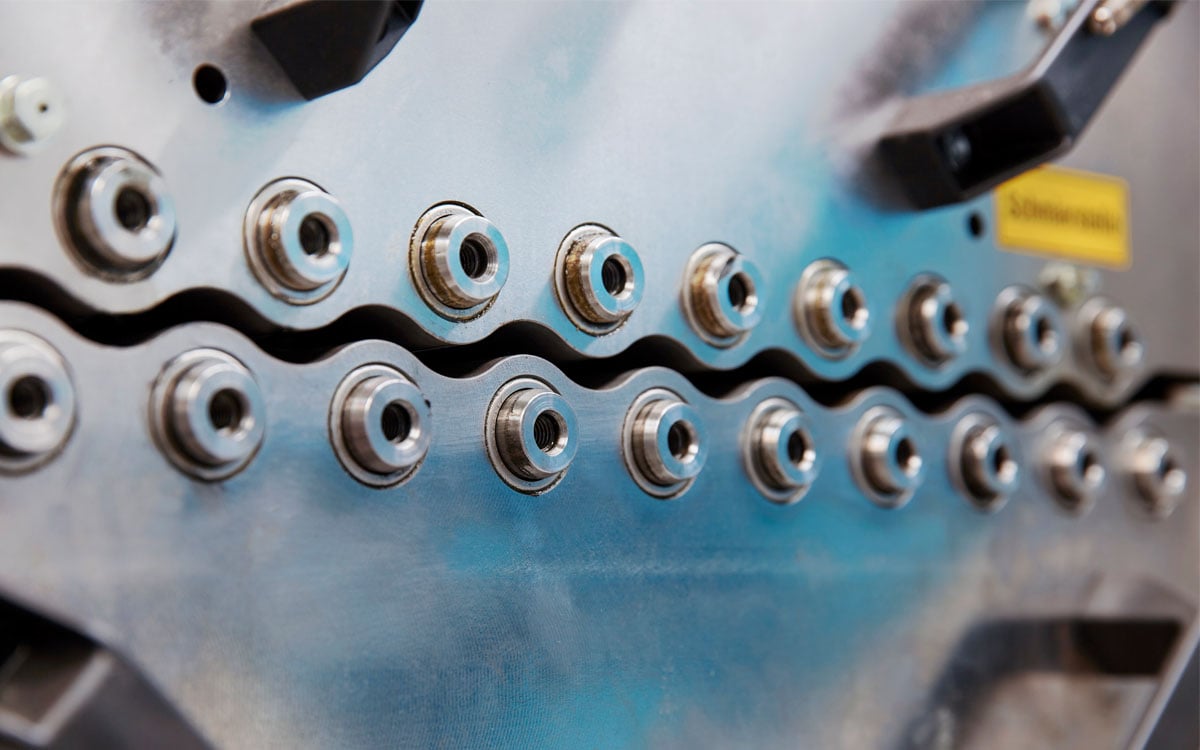
Facts as an overview
- The elastic-plastic alternating bends and the constant reduction in deformation result in a flat and, above all, stress-free sheet metal part.
- Roller levelers can straighten your sheet metal and heavy plates fast and efficiently.
- Graphical touchscreen HMIs enable the correct settings to be made quickly and accurately, while at the same time making the roller levelers easy to use.
Suitable machines
Levelers for flame cut parts and heavy plate
Levelers for stamped and laser cut parts
Our servo-hydraulic roller levelers are specially designed for demanding flattening tasks. Thanks to the hydraulics, the maximum required bending force can be applied safely. The straightening rollers are supported to the maximum by the hydraulics and have a small gap between them. Thanks to the integrated straightening gap control, the straightening gap remains constant during the entire leveling process, even with changing part cross-sections. This means that even challenging sheet metal parts and heavy plate can be leveled precisely and stress-free in the shortest possible time.
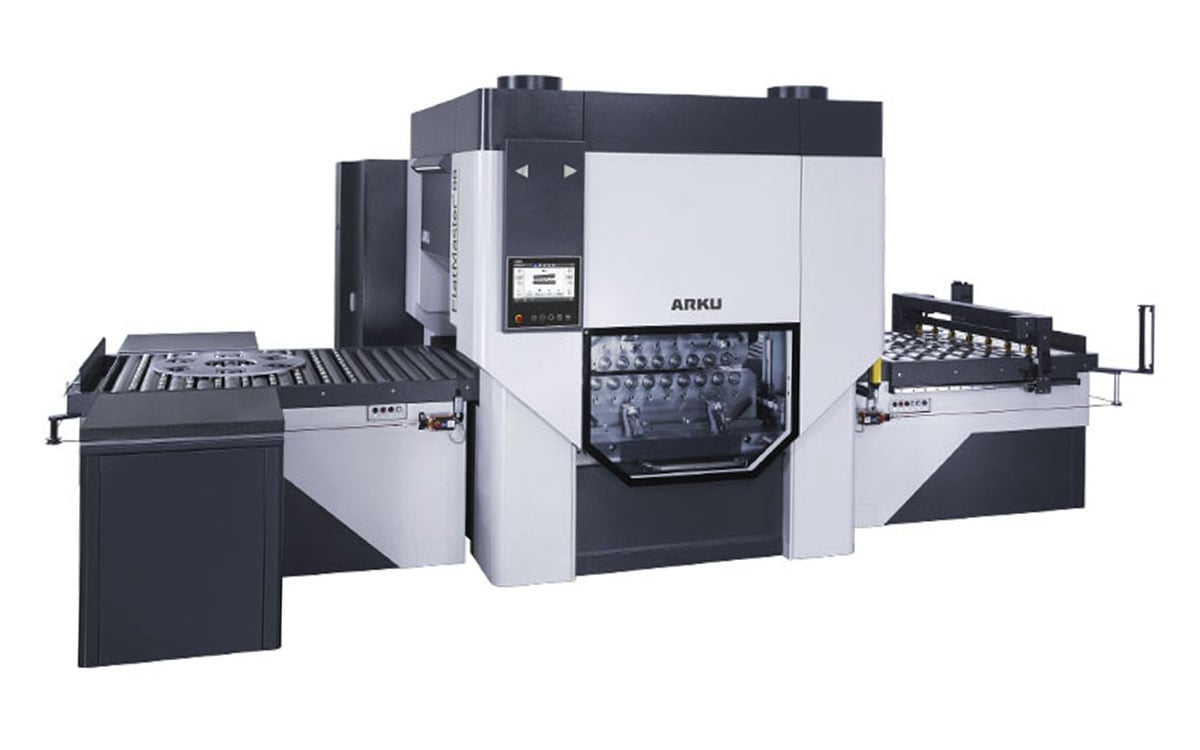
Facts as an overview
- Fast and precise machine adjustments enables flat and stress-free sheet metal parts and heavy plate in seconds.
- High throughput simplifies the leveling of many metal parts without bottlenecks in production.
- Hydraulic overload protection ensures a durable and indestructible roller leveler.
- Power-controlled servo hydraulics save electricity and energy.
- Maximum hydraulic forces enable excellent leveling results even with thick flame and plasma cut parts.
Suitable machines
Levelers for flame cut parts and heavy plate
Levelers for stamped and laser cut parts
What Distinguishes Roller Levelers from Alternative Straightening Methods?
Thanks to their durability and indestructibility, our precision levelers are a reliable and safe investment. They have various advantages over alternative straightening methods:
- Flat and stress-free sheet metal and heavy plate for efficient downstream processing
- Significantly faster and more efficient leveling results than with other straightening methods
- Intuitive machine operation without the need for extensive training
- Subsequent process steps such as cutting, welding or bending become more consistent and accurate
- Reduction of rework and rejects
- Repeatable results, regardless of the employee
- High throughput enables the leveling of many components without bottlenecks in production
- Residual stresses within the material are hardly reduced
- Significantly more time-consuming than compared to a roller leveler
- Processing times of 20 minutes or more per part are not uncommon
- Only extremely experienced employees can use these methods
- Inconsistent flattening results are a common occurrence
Do you require further information?
Do you have a question for ARKU or would you like to receive more information about our products and services? Contact us and we will take care of it. Fast and reliable.