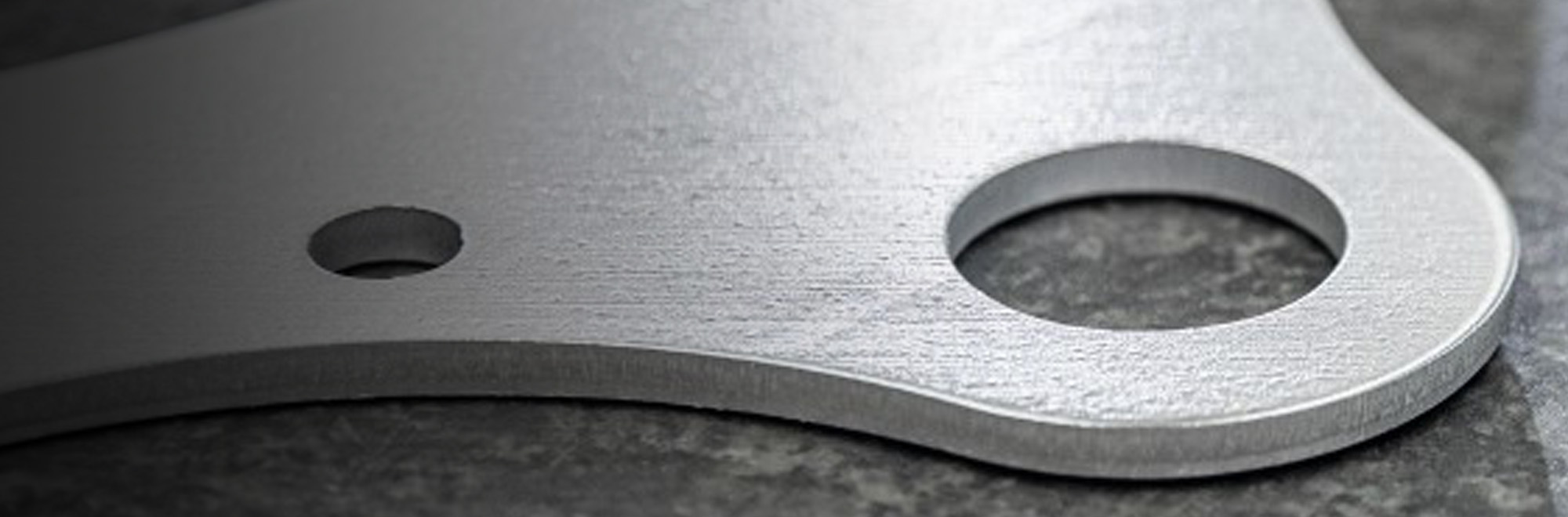
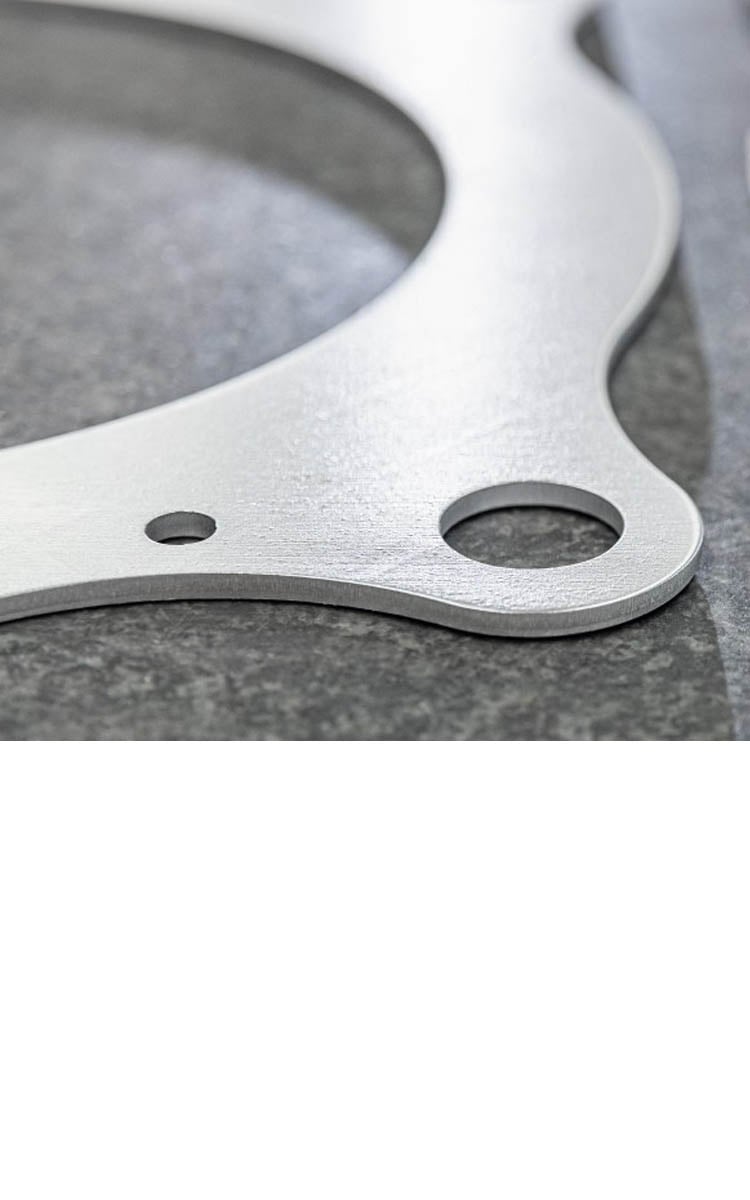
Deburr and edge round sheet metal parts with ARKU: reliable, flexible and double-sided. For metal parts quality ahead of the competition.
Reliable deburring and edge rounding
Laser-cut & Punched Parts Deburring Machines
ARKU offers machines for the deburring, edge rounding and surface finishing of sheet metal parts after laser cutting and punching. These machines can also process the entire sheet metal prior to cutting. Depending on the final requirements, various methods of deburring technologies can be used. The geometry, number of pieces and part dimensions, also have an influence on the machine configuration. The goal is to always achieve consistent, high quality results for deburring and edge rounding of your punched and laser cut parts.
Here you can get an overview of our EdgeBreaker® models in comparison
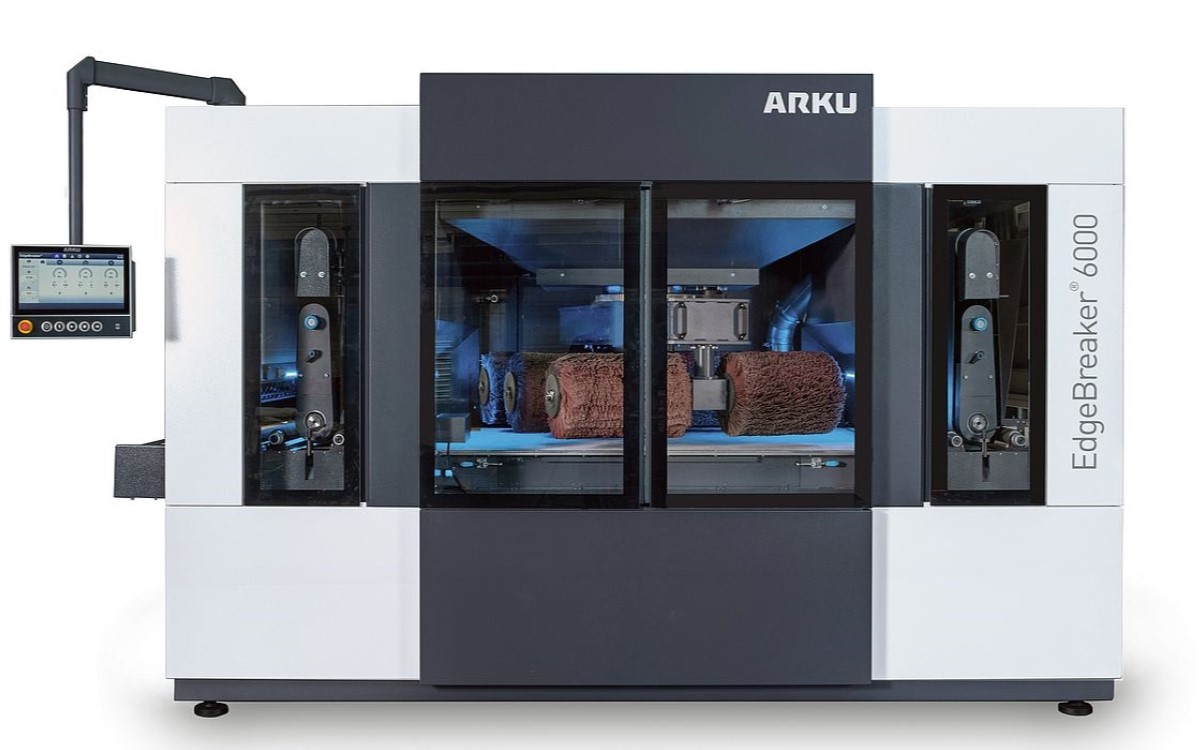
EdgeBreaker® 6000
Flexible all-rounder for any type of laser cut and punched parts. The most versatile of our automated deburring machines for laser job shops.
Material thickness: up to 25 mm.
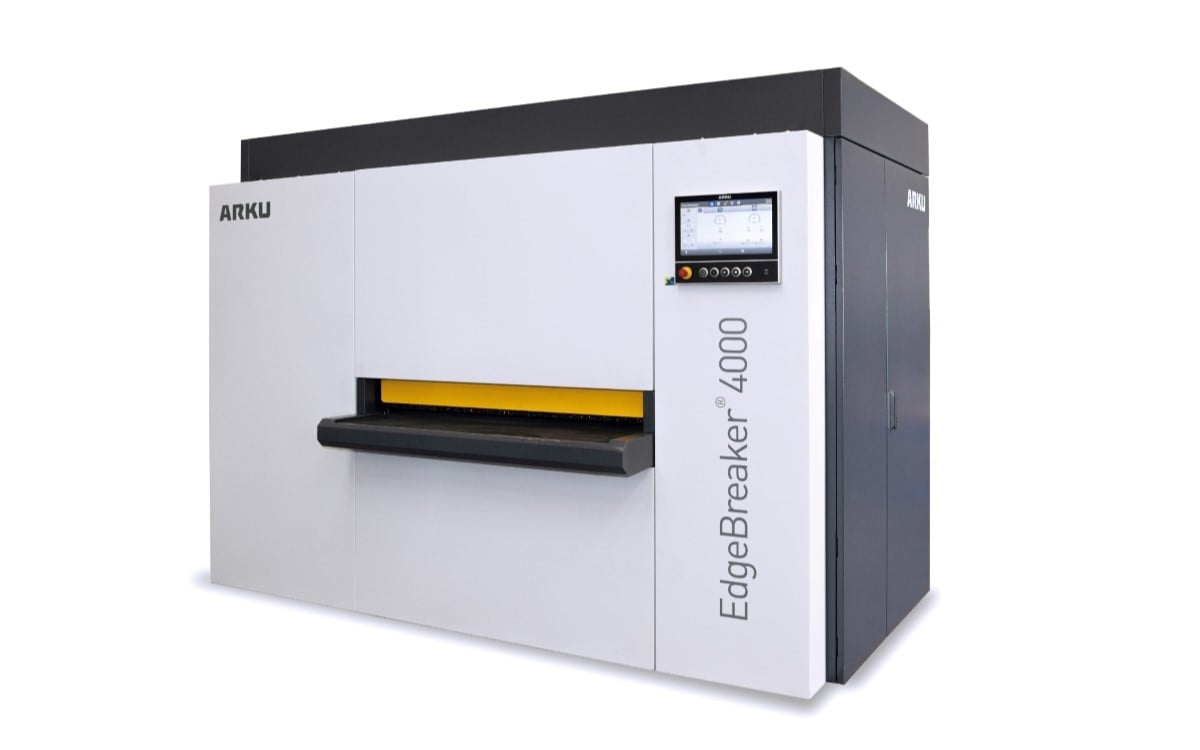
EdgeBreaker® 4000
The ultimate powerhouse for laser-cut parts with a strong burr.
Material thickness: 0.8 - 100 mm.
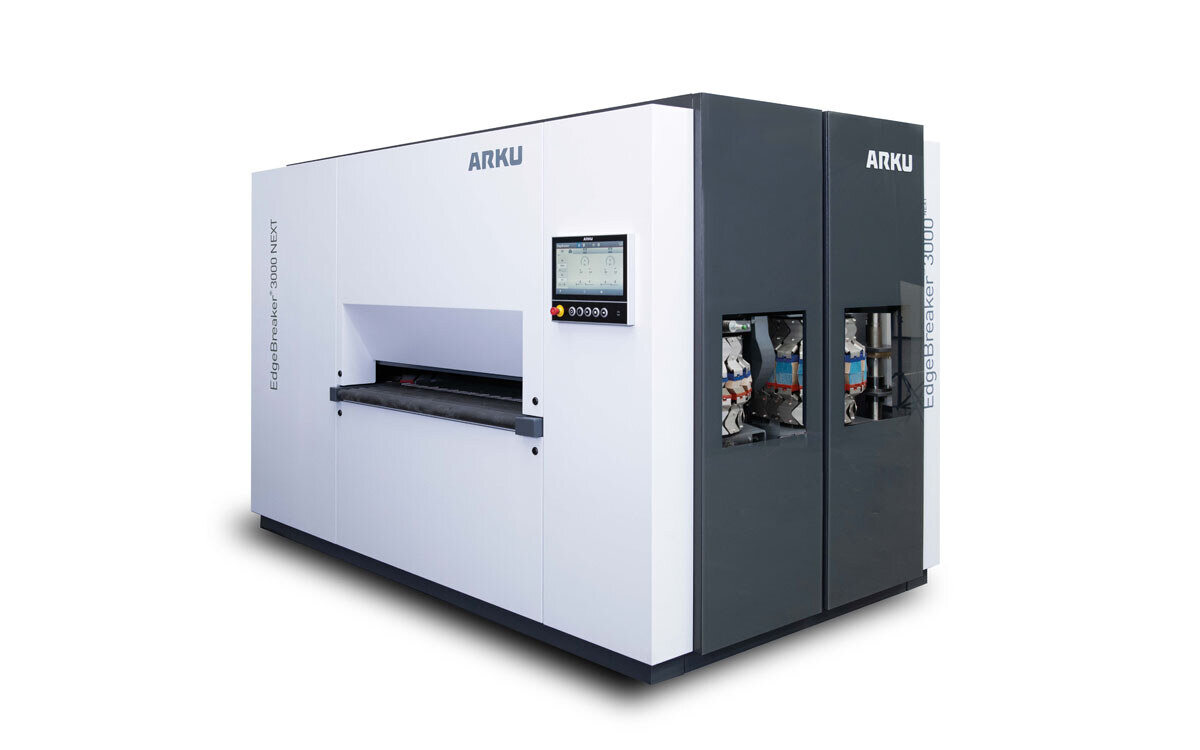
EdgeBreaker® 3000 NEXT
Powerful workhorse for maximum throughput – deburrs and edge rounds top and bottom in a single pass.
Material thickness: 0.8 - 100 mm.
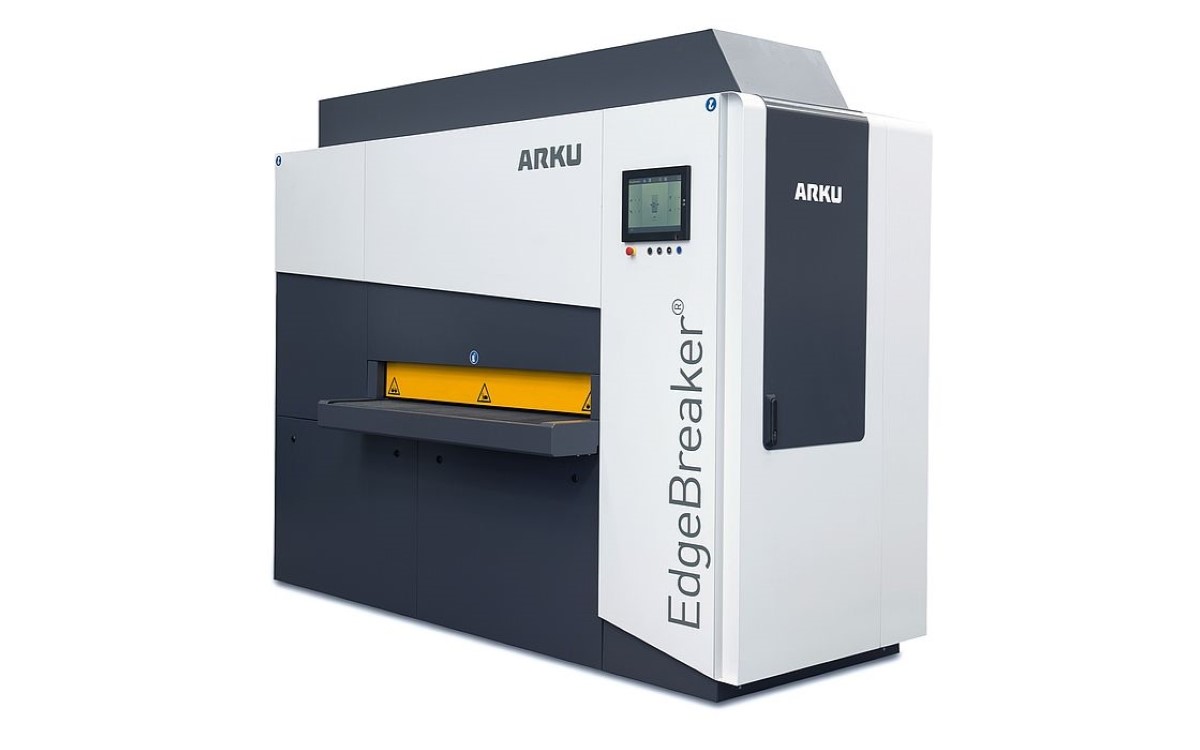
EdgeBreaker® 2000
The double-sided edge rounding expert that can also deburr.
Material thickness: 0.8 - 100 mm.
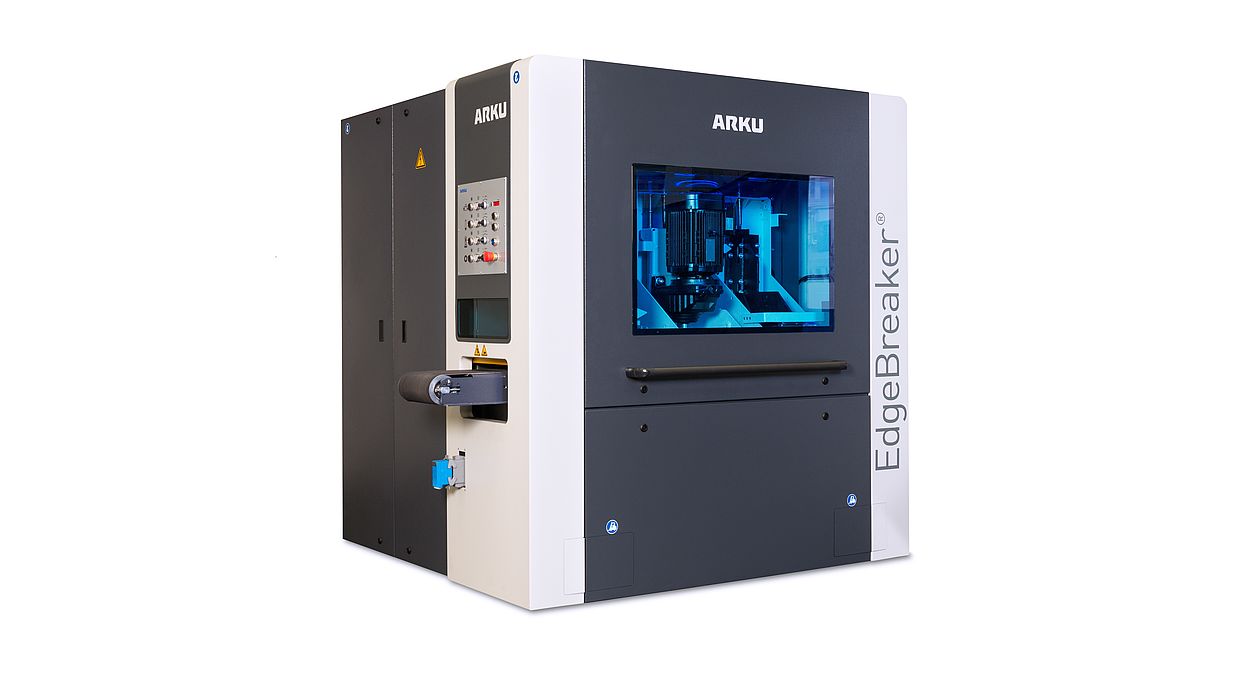
EdgeBreaker® 1000
Specialist for the economic processing of small parts. Deburring, edge rounding and finishing.
Material thickness: 0.5 - 25 mm.
Deburring processes as an overview
Deburring
The burr can vary when punching or laser cutting your materials. Burrs created via laser cutting and punching adhere to the material in various strengths. Therefore finding a comprehensive deburring solution is crucial.
Edge rounding
A good edge rounding result is characterized by removing the sharpness on the edges of your laser-cut or punched materials. This prevents injuries that may be caused by handling the material, while simultaneously improving downstream processing. Furthermore, a radius at the edge of the materials also improves paint adhesion.
Laser oxide removal
If you are cutting via a CO2-laser with oxygen, the EdgeBreaker® series can remove any oxide layers along the cutting edge of the material.
Surface finish
Punched and laser-cut parts often require high demands on the surface. A beautiful surface is a pleasant side effect of the deburring process. In some cases, a specific type of surface finish could be necessary.
EdgeBreaker® Models in Comparison
Processing type | Processes | Material thickness | Max. working width | Dimensions at 1300 mm (L x W x H) |
|
EdgeBreaker® 6000 | single-sided, dry | deburring, edge rounding, oxide removal, surface finishing | 1.0 - 25 mm | 1,300 mm | 4,200 x 2,100 x 2,350 mm |
EdgeBreaker® 4000 | double-sided, dry | deburring, edge rounding, oxide removal | 0.8 - 100 mm | 1,300 mm | 3,100 x 2,200 x 2,200 mm |
EdgeBreaker® 3000 NEXT | double-sided, dry | deburring, edge rounding, oxide removal | 0.8 - 100 mm | 1,300 - 2,000 mm | 3,100 x 2,200 x 2,200 mm |
EdgeBreaker® 2000 | double-sided, dry | edge rounding, oxide removal | 0.8 - 100 mm | 1,300 - 2,000 mm | 3,100 x 1,500 x 2,200 mm |
EdgeBreaker® 1000 | single-sided, dry | deburring, edge rounding, surface finishing | 0.5 - 25 mm | 250 mm | 2,100 x 2,600 x 2,100 mm |