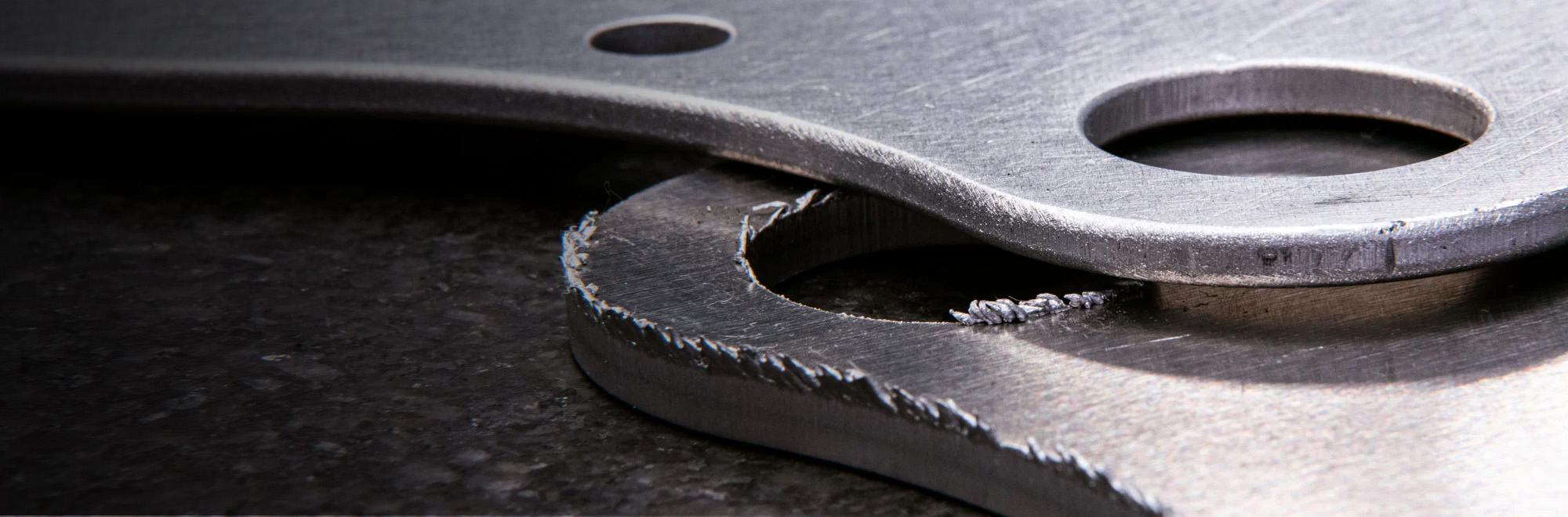
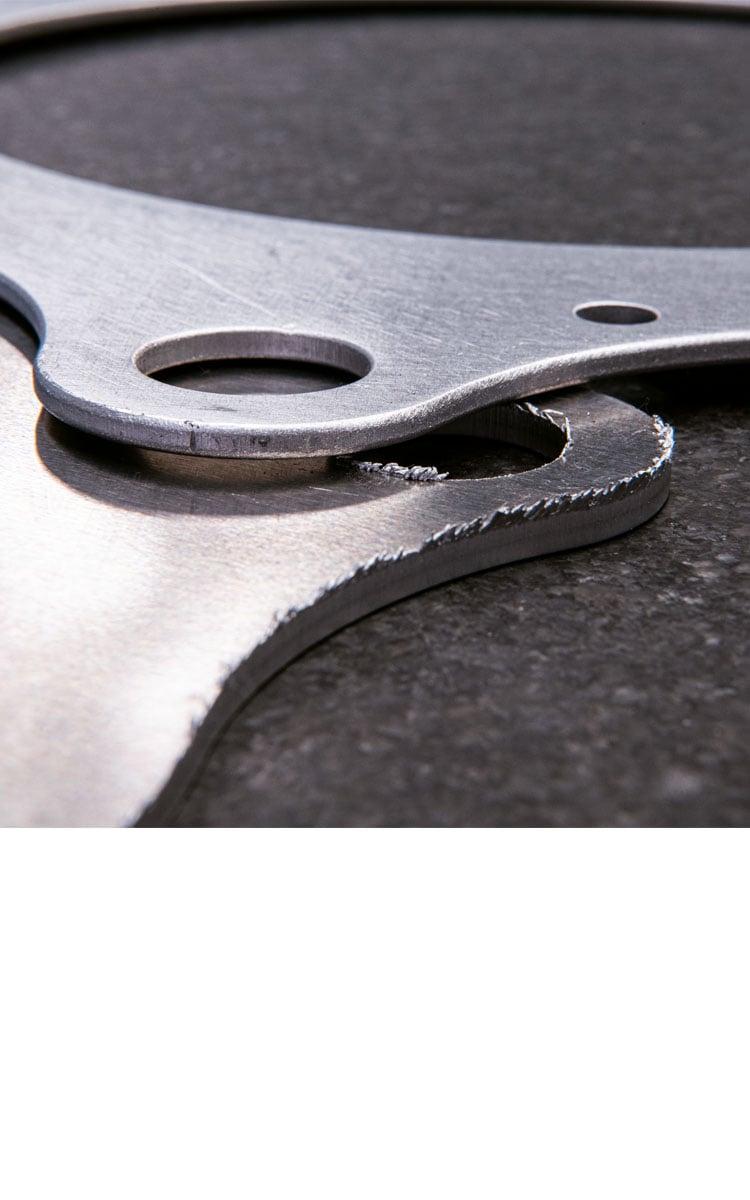
Deburr metal parts, sheets and plates double or single-sided. Save valuable time and money with the optimal deburring solution.
Straight to the machinesDeburring Sheet Metal Parts, Sheets & Plates
Deburring of sheet metal is the removal of protruding metal and sharp edges after cutting. These burrs are tiny pieces of metal typically stuck to the edges. They are caused by cutting methods like laser, waterjet, plasma as well as for punched parts.
How to Deburr Parts, Sheet Metal & Heavy Plate?
Grinding processes are mainly used for deburring sheet metal parts and sheets. Many companies today rely on automated deburring. Modern deburring machines have various processing units that can be equipped with different abrasives. Depending on requirements, different machines and/or configurations are available to achieve the required deburring result for clean metal edges. Thus, modern deburring machines produce clean metal edges for safe and efficient downstream processing of sheet metal parts.
What are the Advantages of Deburring?
Deburring increases the quality of sheet metal parts
Deburred sheet metal parts are a sign of quality. On the one hand, burr-free parts can be seamlessly processed down the line, on the other, they also result in fewer scratches and damage to neighboring parts when stacked.
Deburred sheet metal is more efficient for further processing
Deburring increases the quality of sheet metal. This in turn leads to more efficient downstream processing with time and cost savings. Clean, deburred parts and sheets are easier to assemble, paint and weld. The risk of downstream equipment and tools, such as a precision leveling machine, being damaged by burrs is also reduced.
Deburring protects against machine wear
Clean, deburred parts and sheets reduce the potential wear on downstream equipment. Burrs on the material could potentially damage tools in other machines, for example, a precision leveler.
Deburring with the Grinding Drum
The grinding drum is the strongest deburring tool. This is why the grinding drum is mainly used for heavier plate and parts with strong burrs or light slag. A drum covered with an abrasive belt, presses on the material edges from above. This drum then rotates and oscillates and thus grinds the interfering burrs off the parts. A large diameter and a flexible base under the actual circular drum as well as the abrasive belt, ensure high pressure along all the material edges and an excellent removal rate. The grinding drum has established itself as the leading deburring process for plasma and flame (oxyfuel) cut parts. Even for strong adhering fiber laser burrs the drum is a powerful burr removal tool.
There is a wide variety of different abrasives that can be used in conjunction with a grinding drum. Depending on the grain type, grain size and degree of stiffness of the drum, users can influence the removal rate or the service life of the abrasives. Due to the large diameter of the grinding drum, particularly aggressive abrasives can be used, which underlines its uniqueness in the field of heavy plate and part processing.
Facts at a glance
- The grinding drum is the strongest deburring tool.
- There is a large variety of different abrasives that can be used with the grinding drum.
- The type of grit, the grit size and hardness grade of the abrasives all have an impact on the removal performance or the life of the abrasives themselves
- Due to the large diameter of the grinding drum, particularly aggressive abrasives can be used, which underlines their uniqueness in the area of heavy plate processing.
Suitable machine
Deburring with a Wide Belt
Facts at a glance
- Wide belt units are probably the most commonly used deburring units.
- The sand paper used is available in a large variety.
- Different qualities impact removal performance, the material surface and wear resistance.
Suitable machine
Deburring with Grinding Blocks
Grinding blocks have the advantage that they can deburr sheet metal from above and below in a single pass. This is always useful if the parts cannot (or should not) be turned. Especially if there is burrs or splatters on both sides of the sheet metal, processing double-sided is unavoidable. Deburring double-sided in a single pass ensures considerable process cost savings. The slightly higher tool costs (compared to a wide belt) are therefore more than compensated for.
Grinding blocks are suitable for removing burrs cause by laser cutting and punching. As the metal sheets or parts are held down before and after processing, the process is also more tolerant to some flatness distortions of the parts. For higher removal rates and more stubborn burrs as well as light slag, the grinding drum mentioned above is used instead of the grinding blocks.
ARKU grinding blocks are available in high-quality zirconia alumina and ceramic versions in various grit sizes.
Facts at a glance
- Deburring blocks are suitable for the removal of burrs created in laser cutting and punching operations.
- Since the sheet metal is held secure before and after processing, the process is also more tolerant should parts have warped slightly.
- ARKU deburring blocks are available in high-quality Zircon corundum and ceramics design with various proven grit sizes.