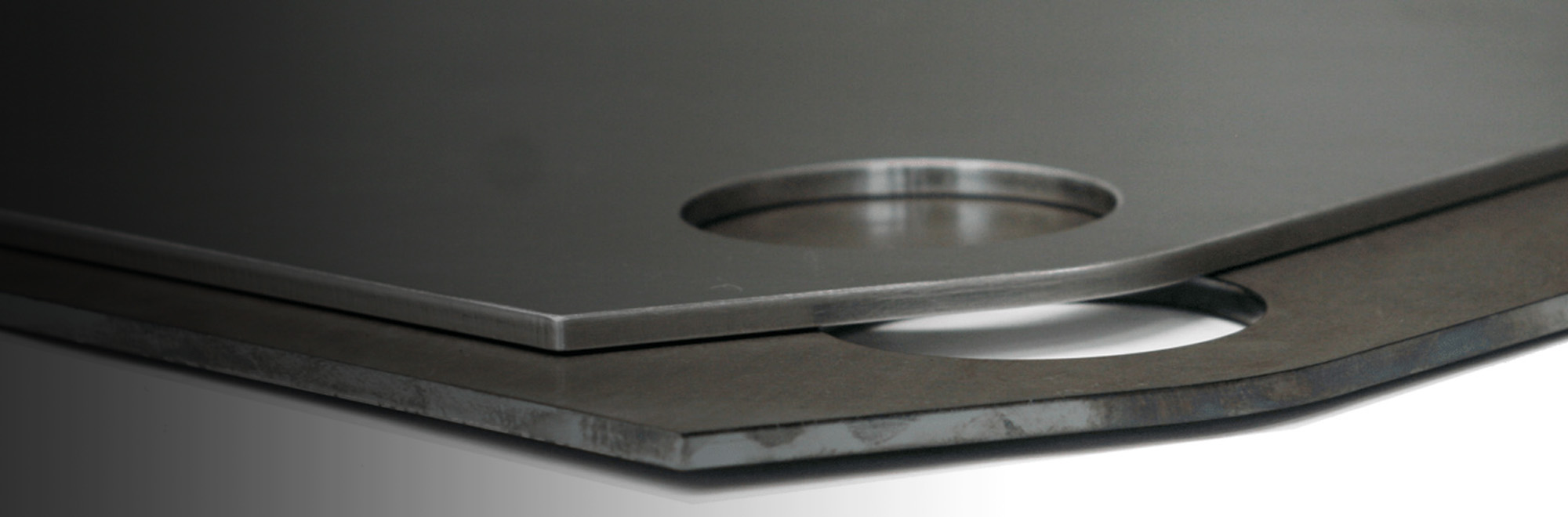
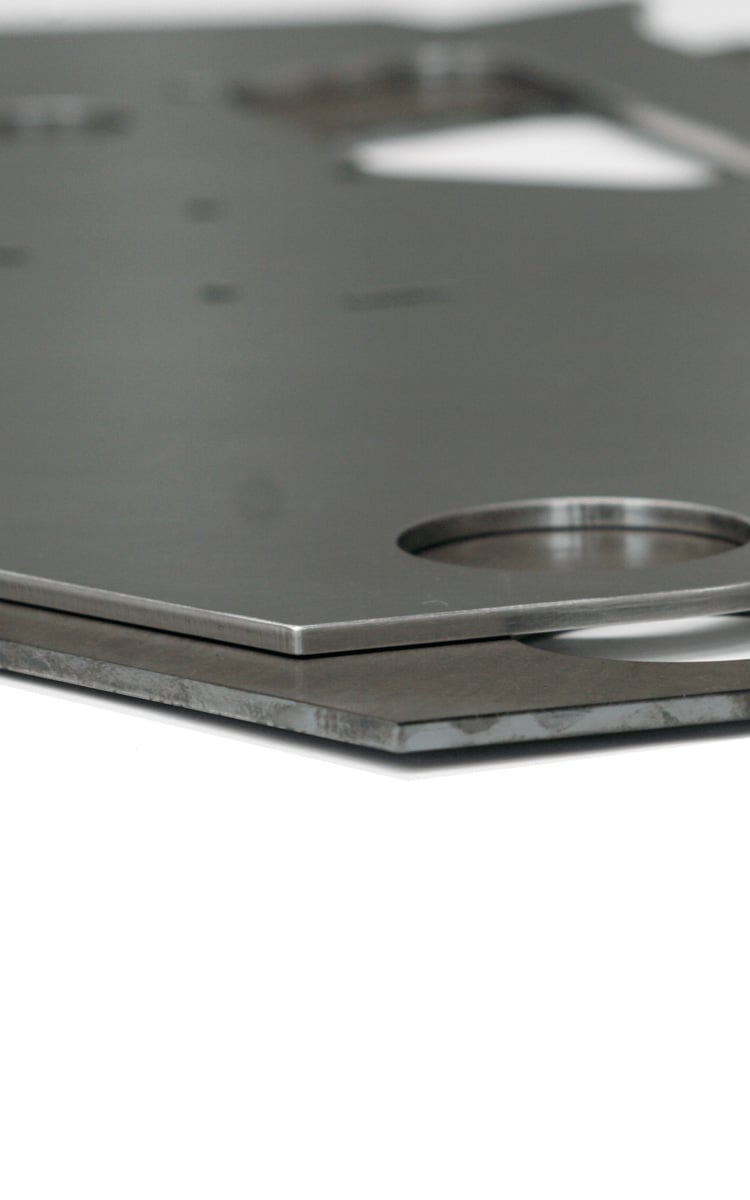
Removing laser oxide from metal parts before coating or welding is imperative for efficient and accurate fabrication.
Straight to the machinesHow to Remove Laser Oxide from the sides of Metal Parts after Cutting?
A laser oxide layer appears along the cutting edge of metal parts. Before coating, welding or other surface treatments, the side of the metal part must be clean of laser oxide layers. These oxide layers occur when laser cutting with oxygen is being utilized that makes the cutting edges oxidize. Metals, especially steel, oxidize very quickly. As enormous heat is being released during cutting, the oxidation process intensifies further.
Although laser oxide layers are very hard, they are not firmly bonded to the underlying material. They can therefore come loose through slight shocks, vibrations or other mechanical methods. This applies not only to aluminum, but any other metal alloy. Removing these laser oxide layers has a positive effect on the quality, durability and functionality of metal parts. Main advantage of clear cutting edges free of laser oxide is to allow proper paint adhesion (coating) without the risk of chipping and rust.
What are the Advantages of Laser Oxide Removal?
Better quality and durability
A laser oxide layer can easily flake off under mechanical stress. Removing these laser oxide layers improves the quality and durability of the metal parts.
Corrosion protection
Even though the laser oxide layer is protecting the material initially, the oxide needs to removed from all sides and surfaces for subsequent painting or coating. Otherwise the risk for rust occurs.
Durable and reliable coating
After removing the laser oxide layer, coatings, paints or adhesives adhere better to the metal surface and edges. This is important for a durable result without any possibilities for paint cracks and potential rust.
Ideal for further processing
Metal parts can be processed more easily without the hard laser oxide layer. For example during welding, bending or painting.
Improved appearance
Traces of laser oxide can impair the visual appearance of metal parts. By removing these laser oxide layers, the surface and the edges of the metal parts becomes clean, smooth and even.
How to remove Laser Oxide with a Machine?
There is a selection of various mechanical processes that can be used to remove a laser oxide layer. The best technical solution is still shot blasting. However, deburring machines can also remove the laser oxide layer from the edges and surface with the right combination of machine tools. These tools include rotary brushes outfitted with steel wires, disc brushes with abrasive bristles, and steel wire brushes. Check out the various methods below.
Laser Oxide removal with Steel Wire Roller Brushes
A roller brush outfitted with steel wires can remove the laser oxide from metal parts as well. These steel wires remove the laser oxide along the cutting surfaces for all the edges for single-sided machines. The more directions the steel wires strike against the metal, the more reliably all sides are free from laser oxide layers.
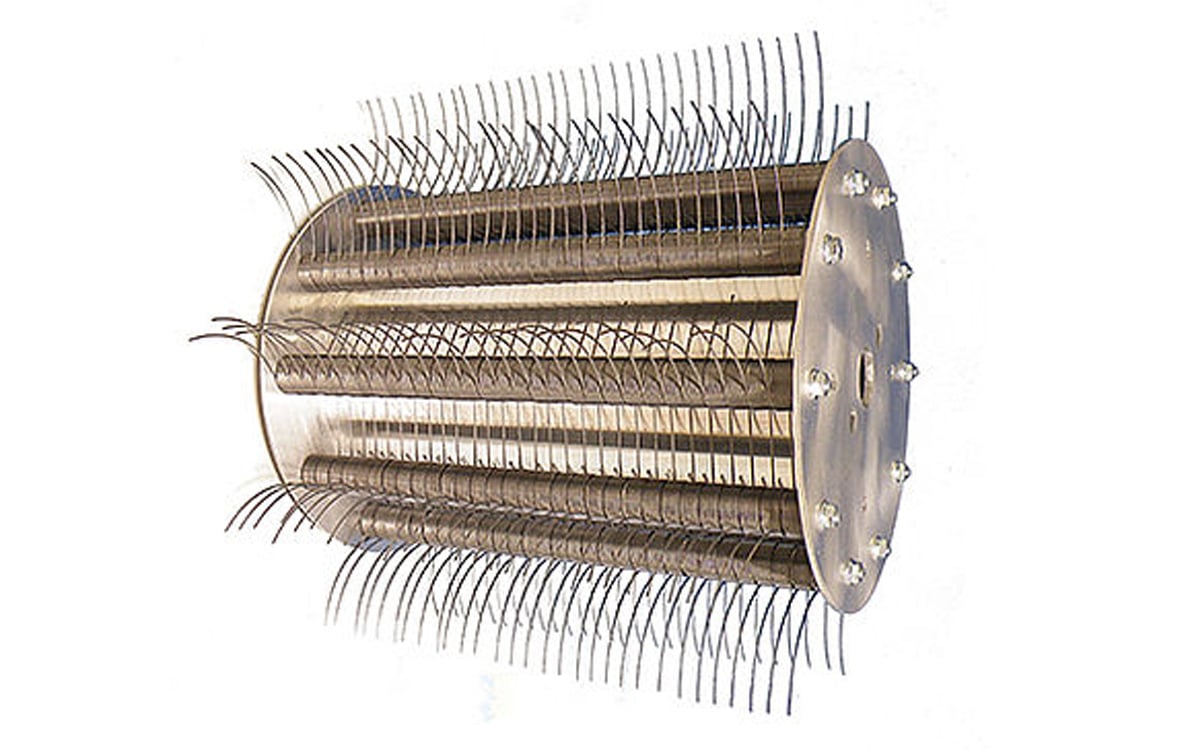
Facts as an overview
- Steel wire roller brushes process the laser oxide layer along the cutting surfaces on the edges.
- Steel wire roller brushes rotate and strike the edges with steel wires from all possible directions.
- Since the steel wires strike the metal parts from all various directions, the more reliably all sides will be free of laser oxide layers.
Suitable machines
Laser Oxide removal with Steel Wire Brushes
The operating principle of deburring blocks outfitted with steel wires is similar to that of the steel wire rotary brushes for laser oxide removal. The brushes (blocks) with steel wires remove the laser oxide from the cutting edges of the metal. Due to the linear movement, the effect is somewhat dependent on the direction of passage. On the other hand, these steel wire brushes have the advantage that they can process sheet metal or thicker parts like plate from above and below in a single pass. This is always useful if the parts cannot (or should not) be flipped over. Processing on both sides in a single pass ensures considerable process cost savings. These steel wire brushes also allow for twice the metal thickness that can be processed.
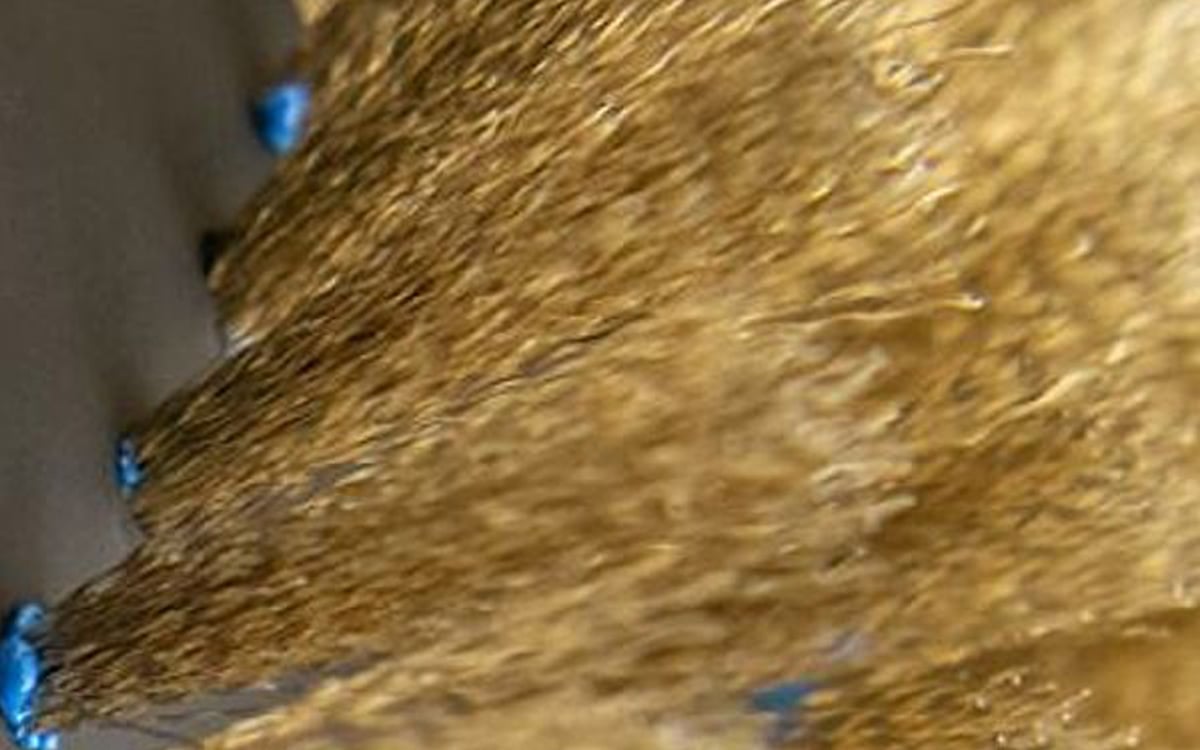
Facts as an overview
- Steel wire blocks can process sheet metal as well as thicker plate double-sided in just a single pass.
- Significant process cost savings thanks to double-sided laser oxide removal.
- Doubles the workable metal thickness.