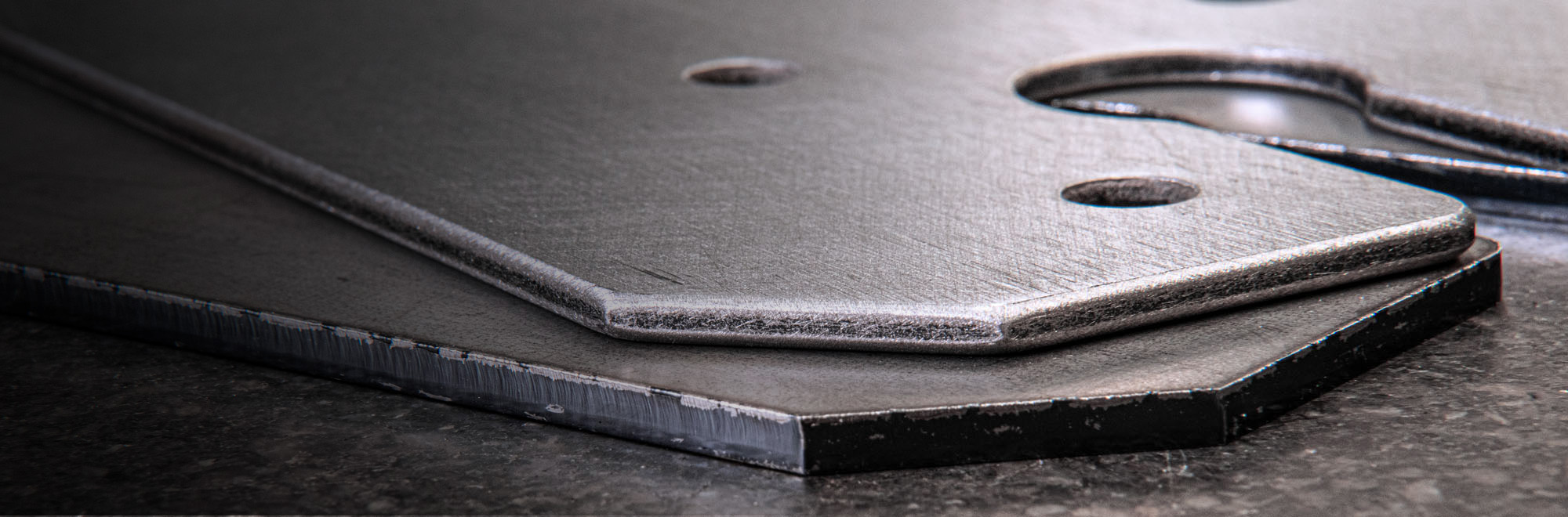
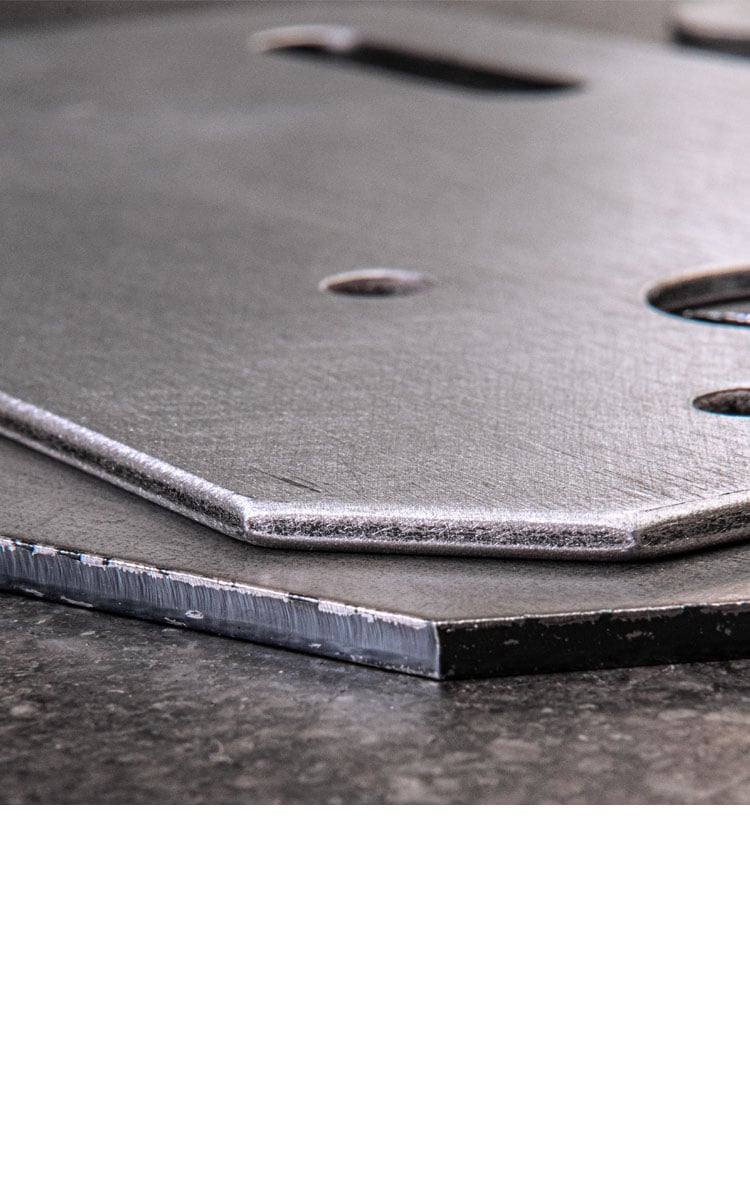
Rounded edges on metal parts, sheets and plates don't just look good. They also have other advantages. Find out more about why edge rounding is essential for metal fabrication.
Directly to the machines?How to Round your Metal Edges
In the world of industrial sheet metal processing, it is common practice to round all sheet edges after cutting. By rounding edges, also known as edge breaking, you can achieve the desired radius on your sheet metal edge. This removes the sharpness from the sheet metal and prepares it specifically for further processing, for example for painting.
In general, edge rounding comes after deburring. During edge rounding, sharp edges are removed and the sheet metal edges are rounded. Depending on the application, it can be important to remove the sharpness of the edge. Larger radii in the range of 0.5 mm are necessary to prepare the sheet metal for reliable coating (painting, galvanizing). Occasionally, radii of up to 2.0 mm are required which can be achieved with ARKU machines as well.
What are the Advantages of Edge Rounding?
Avoidance of injury
Sharp edges on cut sheet metal parts pose a major risk of injury. On the one hand for the user of your products. On the other hand, for your employees who are responsible for handling, assembling and processing sheet metal. Rounded edges prevent injuries when handling sheet metal parts and thus ensure greater safety.
Improved paint adhesion
Liquid coatings and powder coatings have a tendency to peel back on sharp edges. Rounding the inner and outer contours of sheet metal edges ensures that any type of paint or coating can be applied reliably and with long-lasting adhesion. As a result, edge rounding ensures a sealed paint layer.
Corrosion protection
Rounded edges help coatings such as powder coatings, wet paints or galvanised coatings to adhere better. Zinc coatings in particular are more sensitive on sharp edges and can lead to corrosion problems. Standards such as DIN EN 1090 therefore require an edge radius of at least 2 millimetres to ensure corrosion protection.
Longer service life of machines and components
Sharp sheet edges can cause damage to moving cables and hoses in machines, which can lead to machine failures. Rounded edges minimise the risk of these failures and promote a long service life for machines or components.
Edge Rounding with Rotary Brushes
Rotary brushes are equipped with abrasive lamellas. By the rotation of the brushes, the abrasive filaments are pulled across the sheet metal edges and thus achieve their powerful impact on the part edges. While the parts on a conveyor belt are moved under the rotor, the rotary brushes make contact with the part from above. An additional carousel is particularly effective - the so-called rotor - that holds several rotary brushes, which allows for the parts to be uniformly processed from all directions. That is why of all rounding processes, rotary brushes achieve the best and also the most consistent edge rounding results.
Facts at a glance
- Rotary brushes are tools that achieve the best possible edge rounding.
- Up to a 2.0 mm radius can be achieved with a rotary brush.
- The lamellar shape, the type of abrasives and the grit size influence the edge rounding degree on the part.
- Coarse grits have excellent removal performance, but also leave a rough surface.
- Fine grits remove less, but can also handle small parts and leave a smoother surface.
Suitable machines
Edge Rounding with Disc Brushes
Disc brushes are units that are often used in edge rounding operations. Operation and set up are easy to understand. Thus, machines with disc brushes could also be implemented relatively cheap. These are often single-sided machines, which use a conveyor to push the parts through the machine under one or more of the top-acting disc brushes. The tools rotate and strike the parts at the edge. The discs with abrasive filaments are usually mounted stationary if the machine is narrow. Although, they can also cover larger surfaces (and thus larger passage widths) by oscillation or by additional movements.
The disc tools come in a variety of designs. ARKU uses disc brushes in the EdgeBreaker® 1000 for small parts processing. Unique: The EdgeRacer® uses these tools also in machines that process double-sided, such as in the production of computer cases.
Facts at a glance
- Disc brushes deliver relatively uniform results.
- They have limits in terms of life, impact on inner contours and removal performance.
- Single-row or multi-row arrangements of the abrasives on the disc define the hardness grade of the brush.
- The choice of different abrasives or particle sizes impact surface or removal performance.
Suitable machines
Edge Rounding with Rounding Blocks
Like the deburring blocks for deburring, also edge rounding blocks have the advantage that they can process the sheet metal from the top and bottom in a single pass. Typically, this is almost always the most economical edge rounding process because it is fast. The parts are held down by pressure rollers and guided through the machine. Circulating belts guide the tools (edge rounding blocks) double-sided across the materials. Also slightly warped sheets and sheet metal parts are reliably rounded, all while the part is securely fixed. However, double-sided processing requires a minimum parts length. The edge rounding blocks strike the parts perpendicular to the passage direction. Edges that are hit head-on are rounded slightly more than edges that are running parallel to the tool movement.
For many applications, this type of edge rounding is the most economical alternative because the tools process double-sided.
Facts at a glance
- Edge rounding blocks can process the sheet metal from the top and bottom in a single pass.
- The edge rounding blocks are available in different designs.
- Abrasives, grits and design can vary depending on the job.
- Edge rounding blocks feature a quick-change system to quickly replace the blocks.